Architectural Ceramic Assemblies Workshop
Handel Architects was proud to participate in the Architectural Ceramic Assemblies Workshop, sponsored by Boston Valley Terracotta and SUNY Buffalo.
The Architectural Ceramic Assemblies Workshop brings together fabricators, architects, ceramicists, and engineers to promote innovation through collaboration with one of the world’s oldest building materials. The Handel Architects team, led by Associates Paul Lenke, Stefan Di Leo and Jonathan Morefield, were supported by a variety of engineers and artists, including DeSimone Consulting Engineers and The Matter Factory. Thanks to everyone who offered their support.
What is ACAW?
Architectural Ceramic Assemblies Workshop, known as ACAW, is the driving force behind architectural ceramic innovation. Created by Boston Valley Terra Cotta with support from the University at Buffalo School of Architecture and Planning, the ACAWorkshop teaches participants about terra cotta manufacturing and the prototypes and processes explored at ACAW have carried into real-world projects
Our Concept
We worked with a large group of creative minds within the office to
generate a variety of ideas, with a focus on two major ideas: 1) how to
develop a flexible exterior building cladding system with terra cotta,
and 2) how to develop a cladding that would be highly sustainable. Our
question: could one of the world's oldest building materials be
rethought for exterior cladding in a way that would support the
industry's efforts to combat climate change?
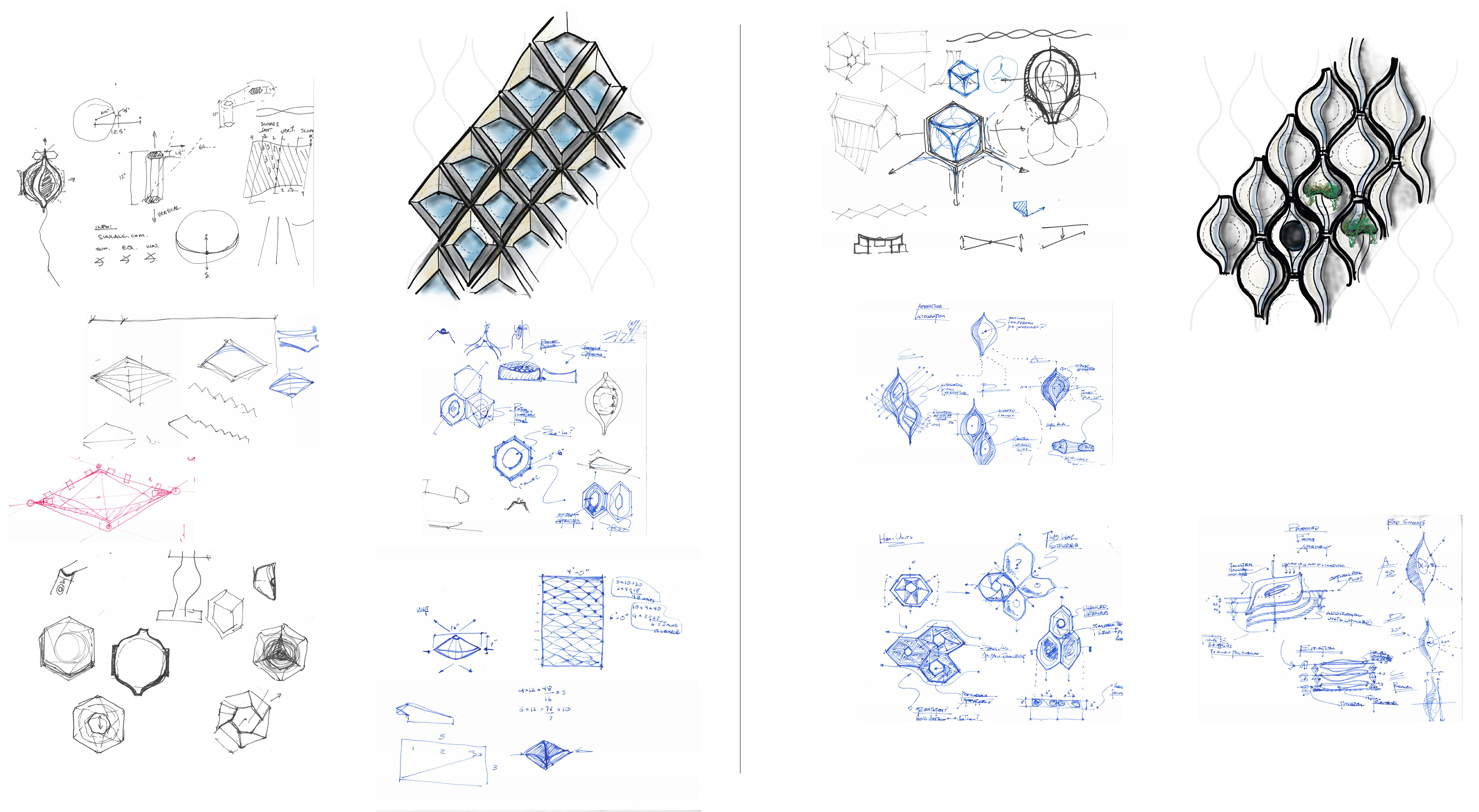
A number of tensile concepts were explored.
The team explored a number of ways to organize and support the facade system and settled on a cable net that uses tension to capture the terra cotta units within it.
This system allowed us to drastically reduce the amount of aluminum and the number of contact points back through the thermal/moisture barrier of the building exterior. Perhaps the most exciting discovery was the system’s ability to be manipulated into more complex ruled surfaces. We then began to explore how we could use the system geometry to further enhance its sustainable characteristics, or design/shape the terracotta itself to further enhance its sustainable characteristics.
We studied the above questions extensively, and talked with many scientists, engineers, and ceramicists on possible solutions. Approaches we studied included photocatalytic air filtration, organic solar PV glazing, green walls and rain water collection, as well as exterior wall cavity ventilation.
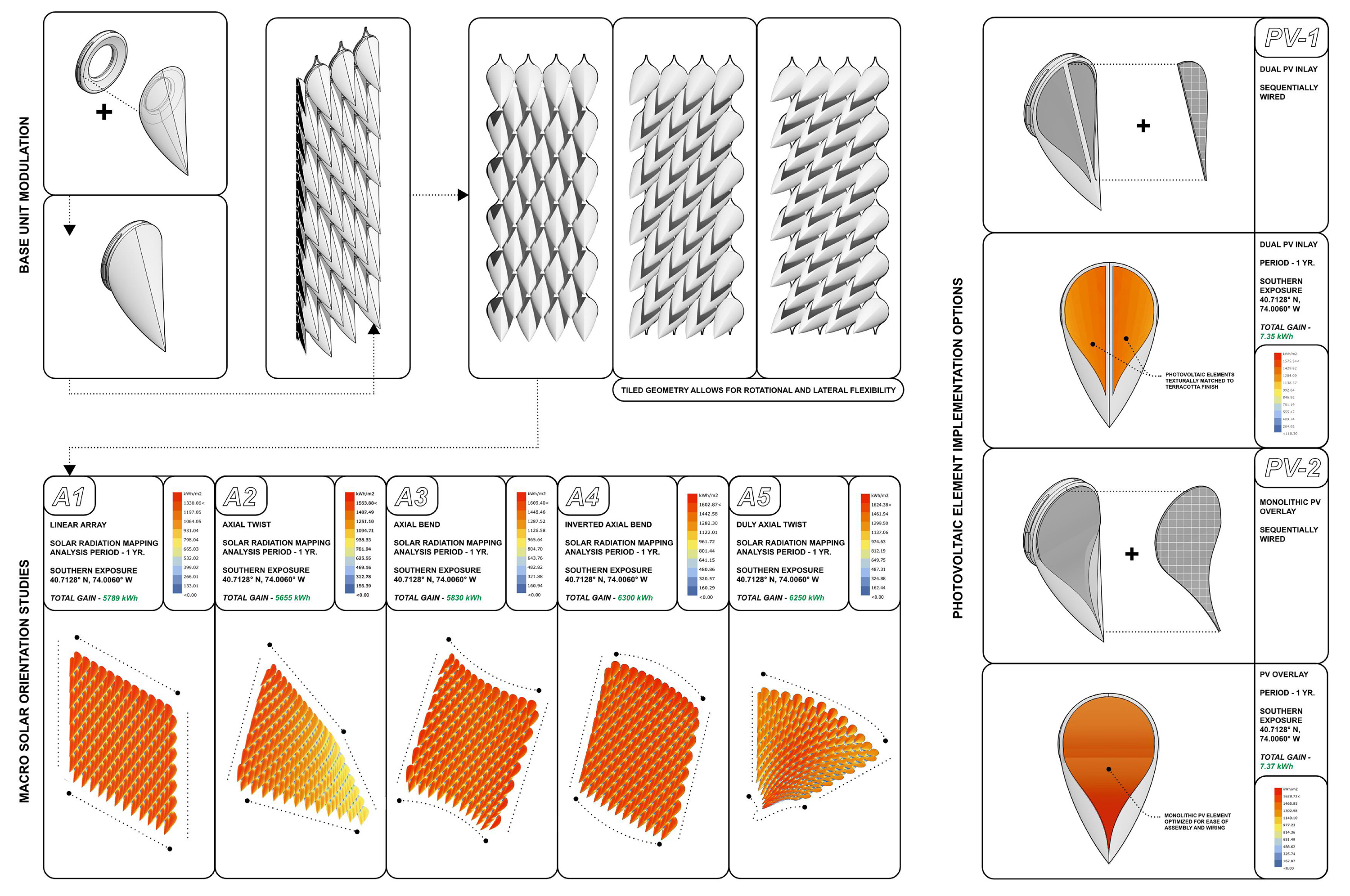
Examples of the system performance studies done during this process.
Tensile Options
In collaboration with DeSimone Consulting Engineers, we evaluated two main tensile net structures: 1-way gravity loaded tensile system and 2-way pre-tensioned tensile system. After investigation and development of both systems, we found that the 2-way system was a much better fit for exterior applications.
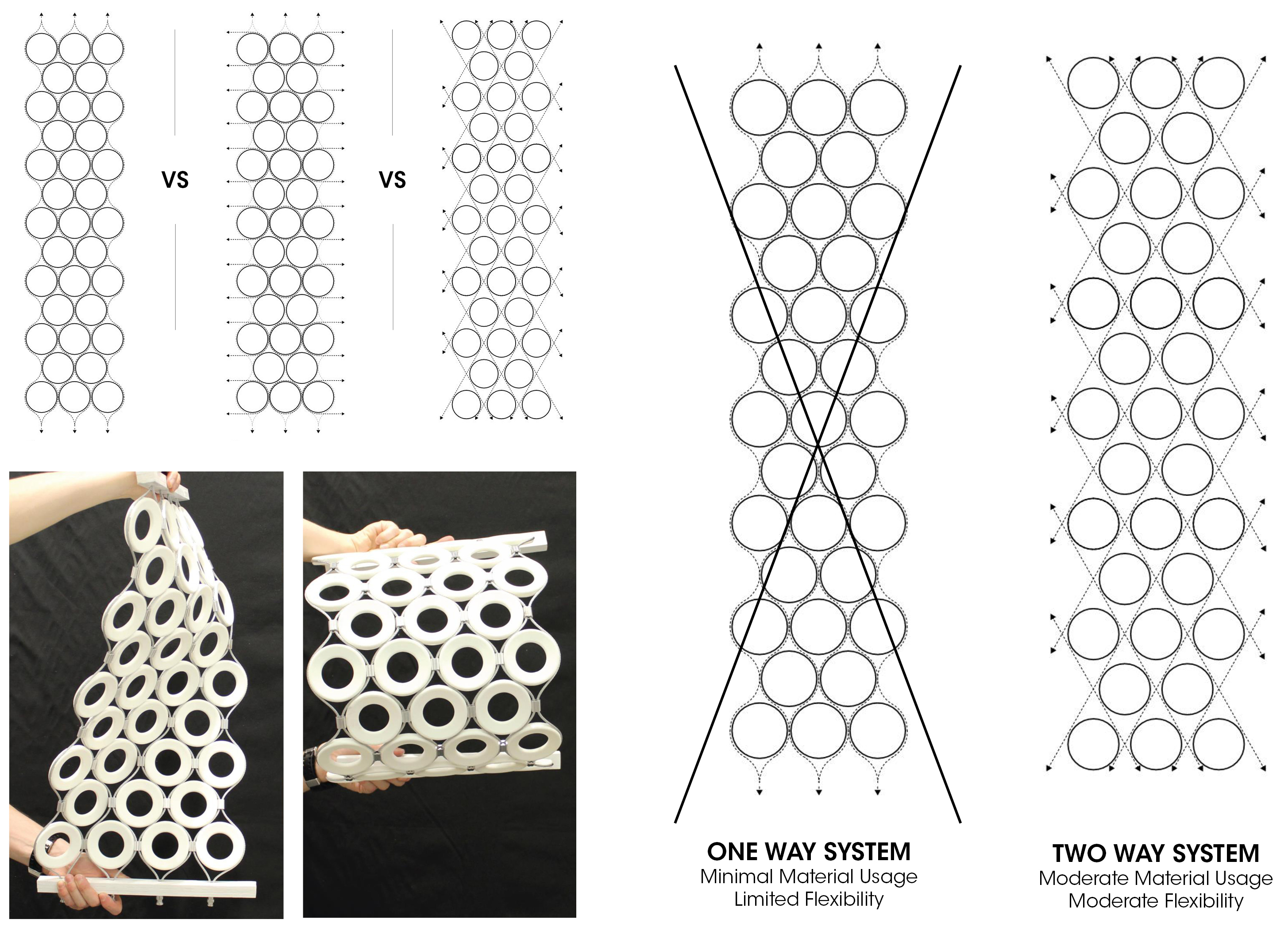
Tensile net structures were designed and built.
Terracotta Geometry
In the development of the exterior geometry, we were inspired by the skin of reptiles: could the protective and performative functions of the reptiles' scaled skin be replicated? We pursued a shingled/scaled shape for the terracotta units that allowed the design to shed wind/water like a traditional rain screen cladding system.
One of the major breakthroughs in the design development process was the realization that by pivoting/rotating the terracotta scale, we could dilate the system to create transparency in the façade; bringing light into the interior spaces where glazing is provided behind. Not only could this be achieved within the same system, but through a single scale through rotation. This allowed the system to be even more dynamic/flexible while only using one ram-pressed terracotta scale geometry, functioning as both rain screen cladding and brise soleil.
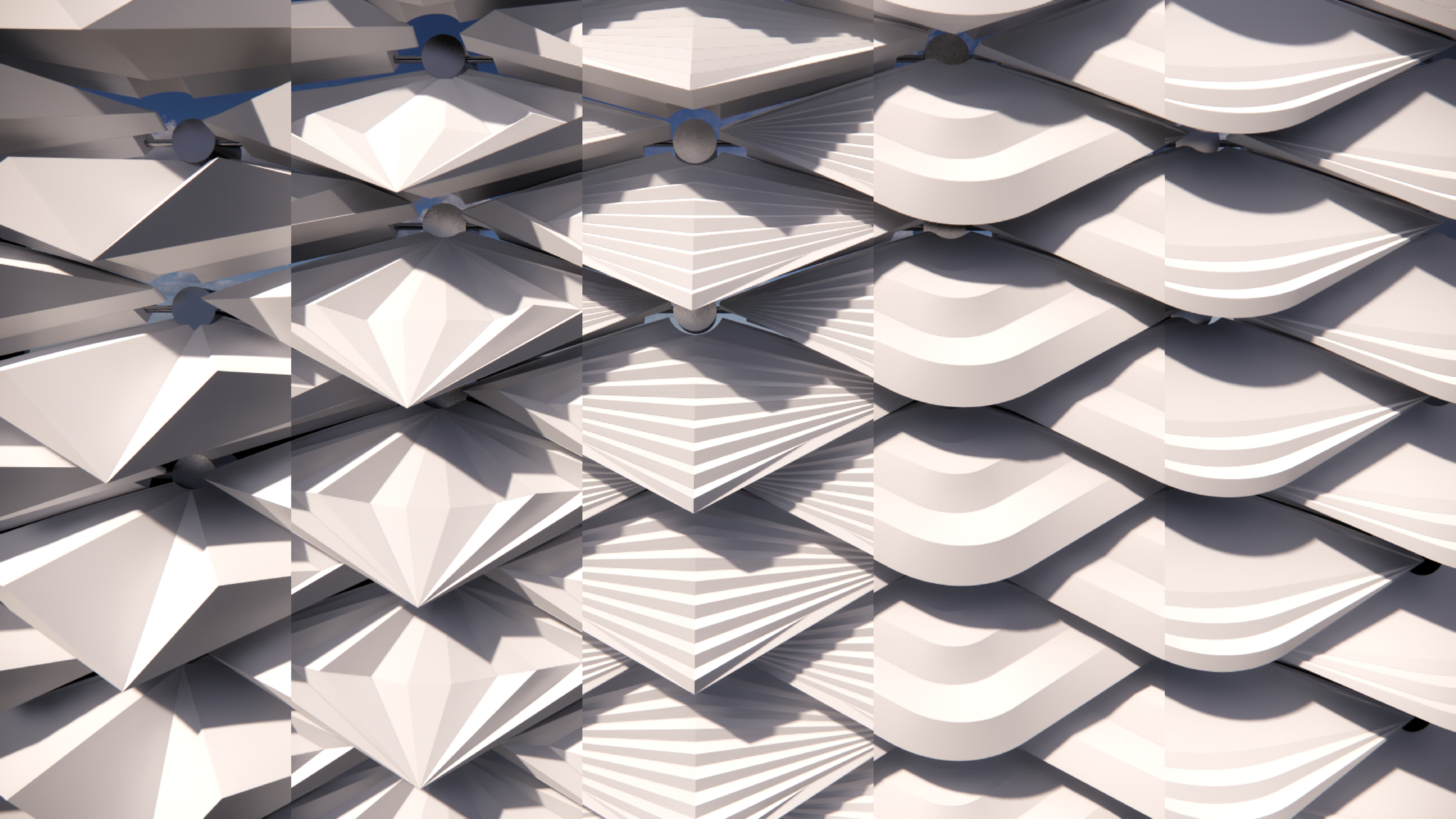
A compilation of shape exercises studied while developing the final terracotta geometry.
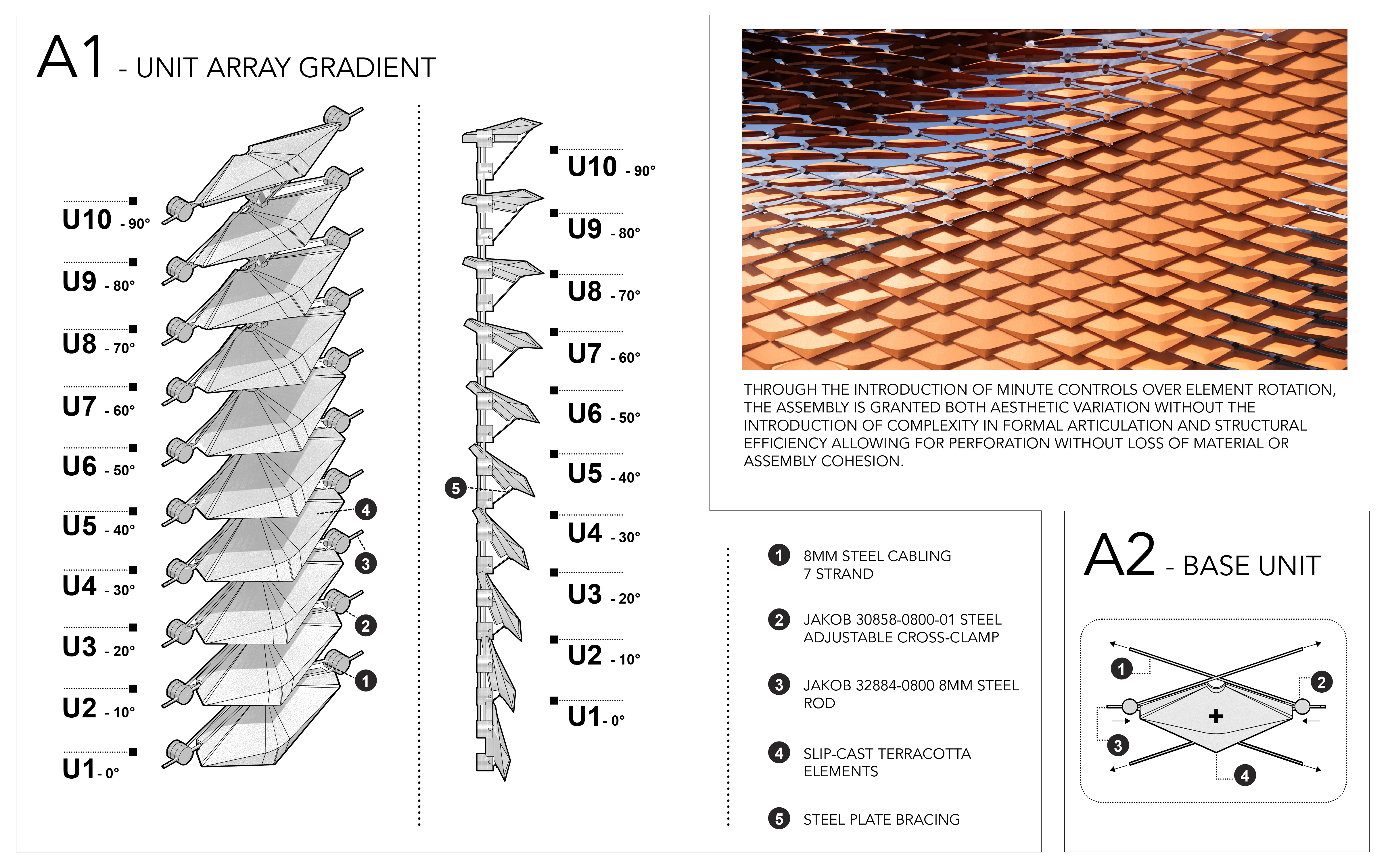
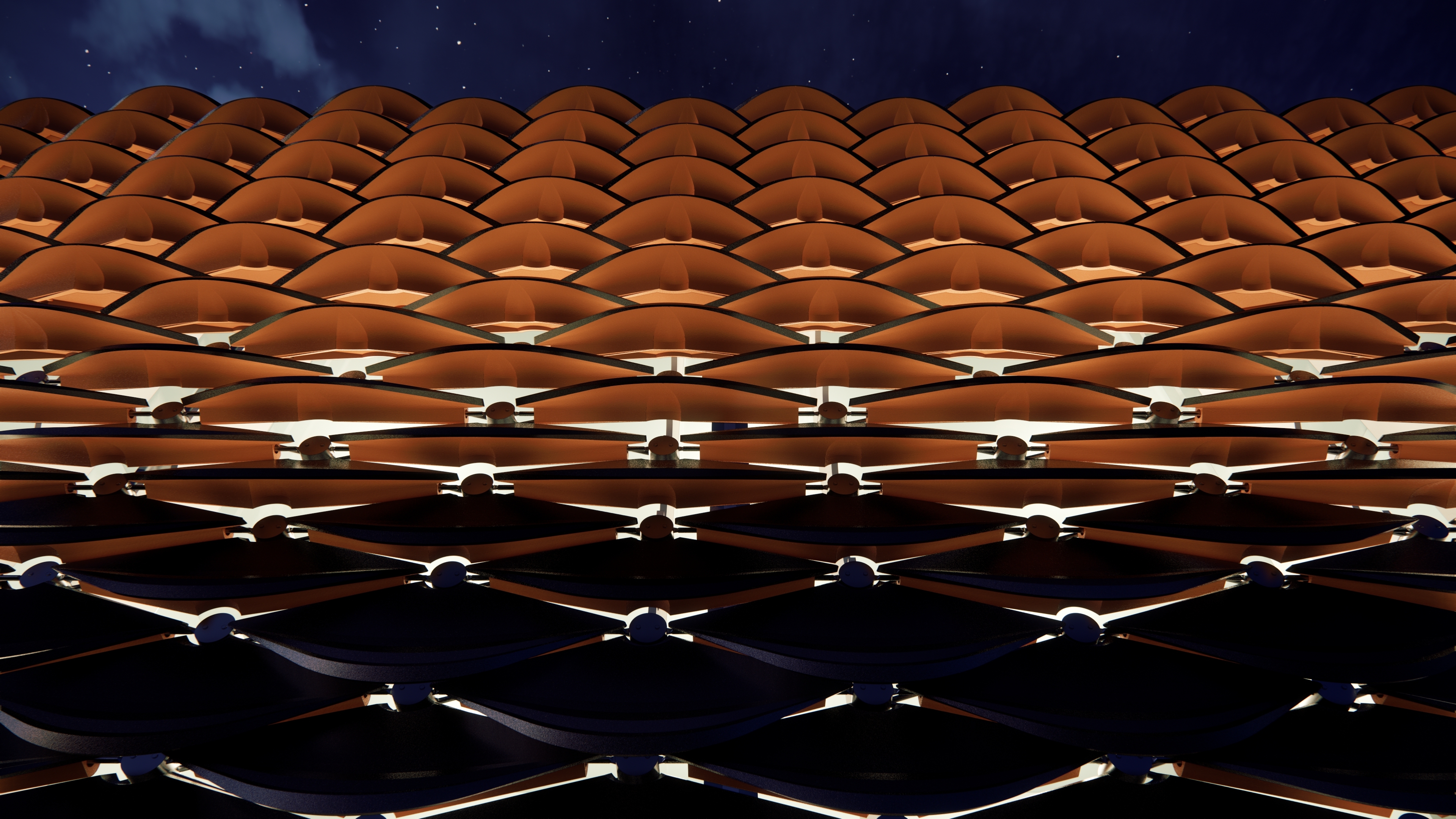
A dramatic view of the system dilating, showing the natural clay color underneath.
The final geometric development focused on interaction with daylight, and facilitating the rotation of the single terracotta scale through the tensile cable system.
For the sake of ACAW, we developed a solution that utilized primarily off-the-shelf hardware. If this prototype were to be developed and engineered further, we would move towards a more custom fabricated solution which would require less components and materials. We developed the hardware mechanisms to utilize a 2-way cable clamp to which the terracotta units were attached at varying angles using preset eye-end bolts.
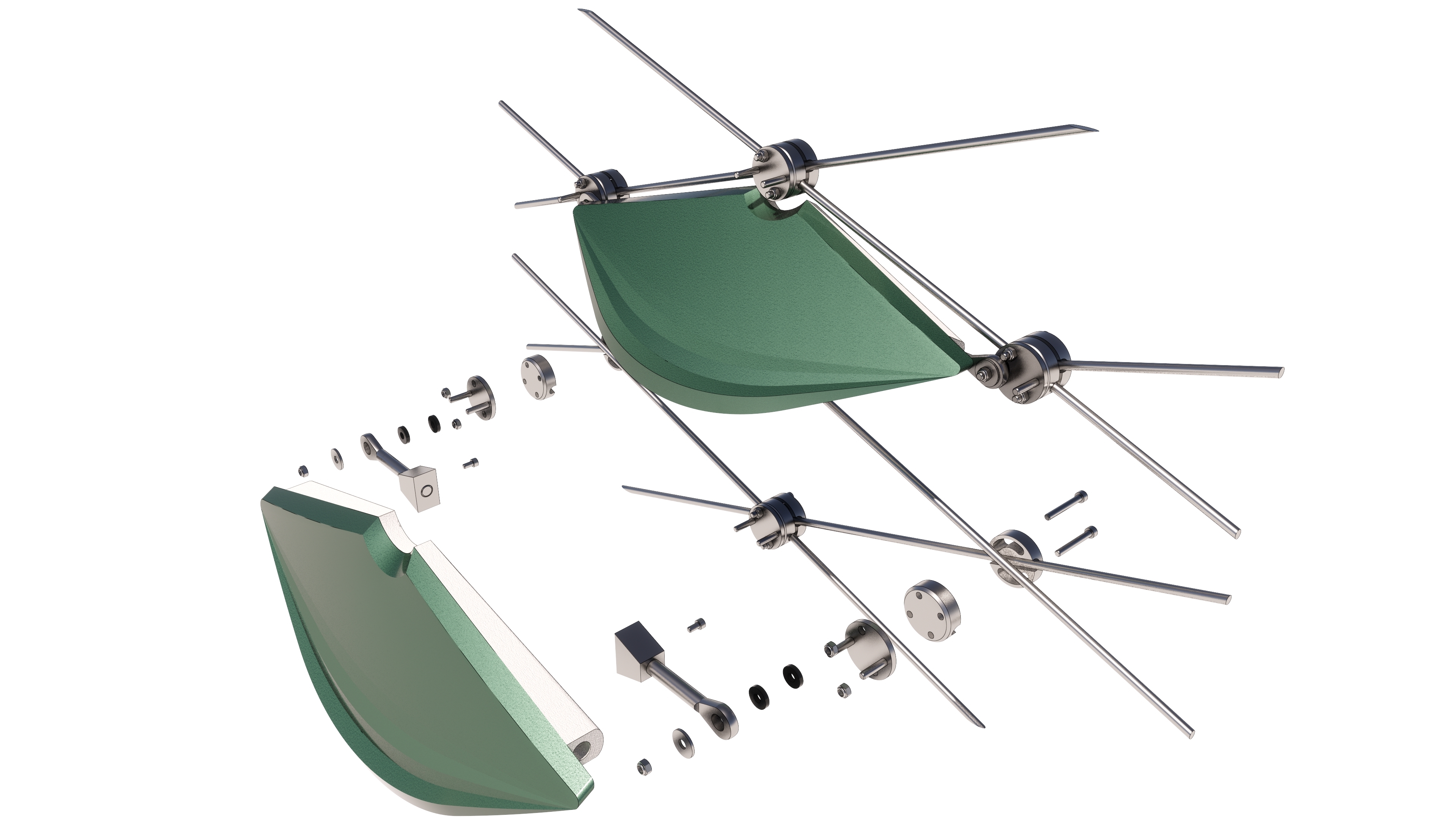
Fabrication
Initially, we tried shaping the pieces using the slip cast technique, which involved pouring liquid clay into a plaster mold, as seen below.
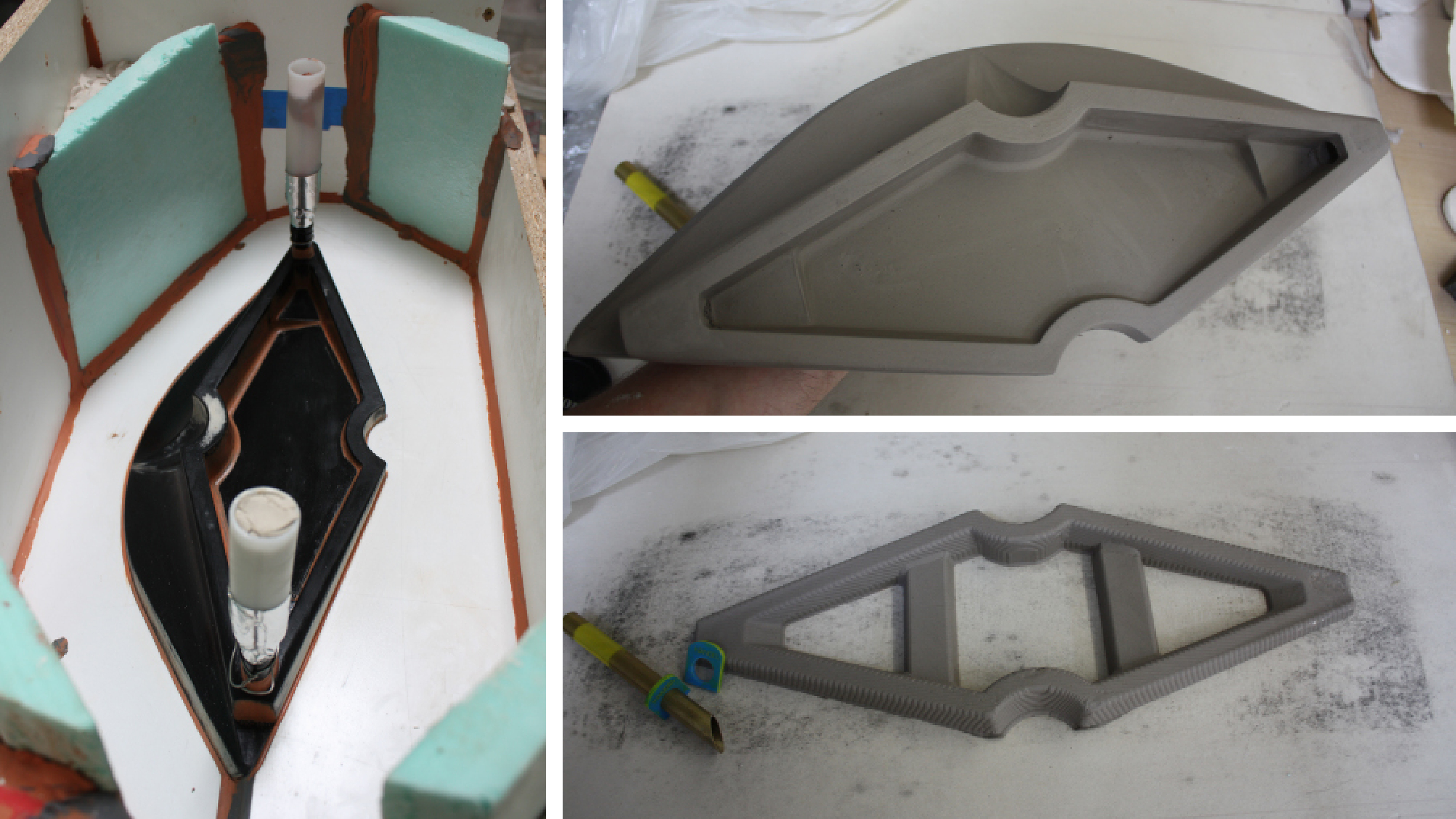
The final shaping of the terracotta module was designed to be ram-pressed, which allowed it to be fabricated at an industrial scale.
When ram-pressing, the clay body is placed in-between two sculpted molds. As the press activates, the top mold presses downward into the bottom mold compacting the clay into the desired shape. Minor post-processing is then done to hollow out the pieces in order to accommodate the attachment hardware.
The ram-pressed modules before they are taken to the kiln for their first firing.
The light-scattering effects in the wings of butterflies and the exoskeletons of beetles inspired the glazing design.
We worked closely with Andy Brayman of The Matter Factory to
deconstruct the color-shifting phenomenon that initially captivated us.
After weeks of experimentation we honed-in on two distinct iridescent
glazes. The primary glaze is dark green color at its base and
color-shifts with view-angle to a metallic bronze when viewed in the
oblique. The secondary glaze is more opalescent and subtle preserving
the visibility of the clay body underneath. As the light source moves,
the thin iridescent coating obscures the base tones and resembles a rich
otherworldly landscape.
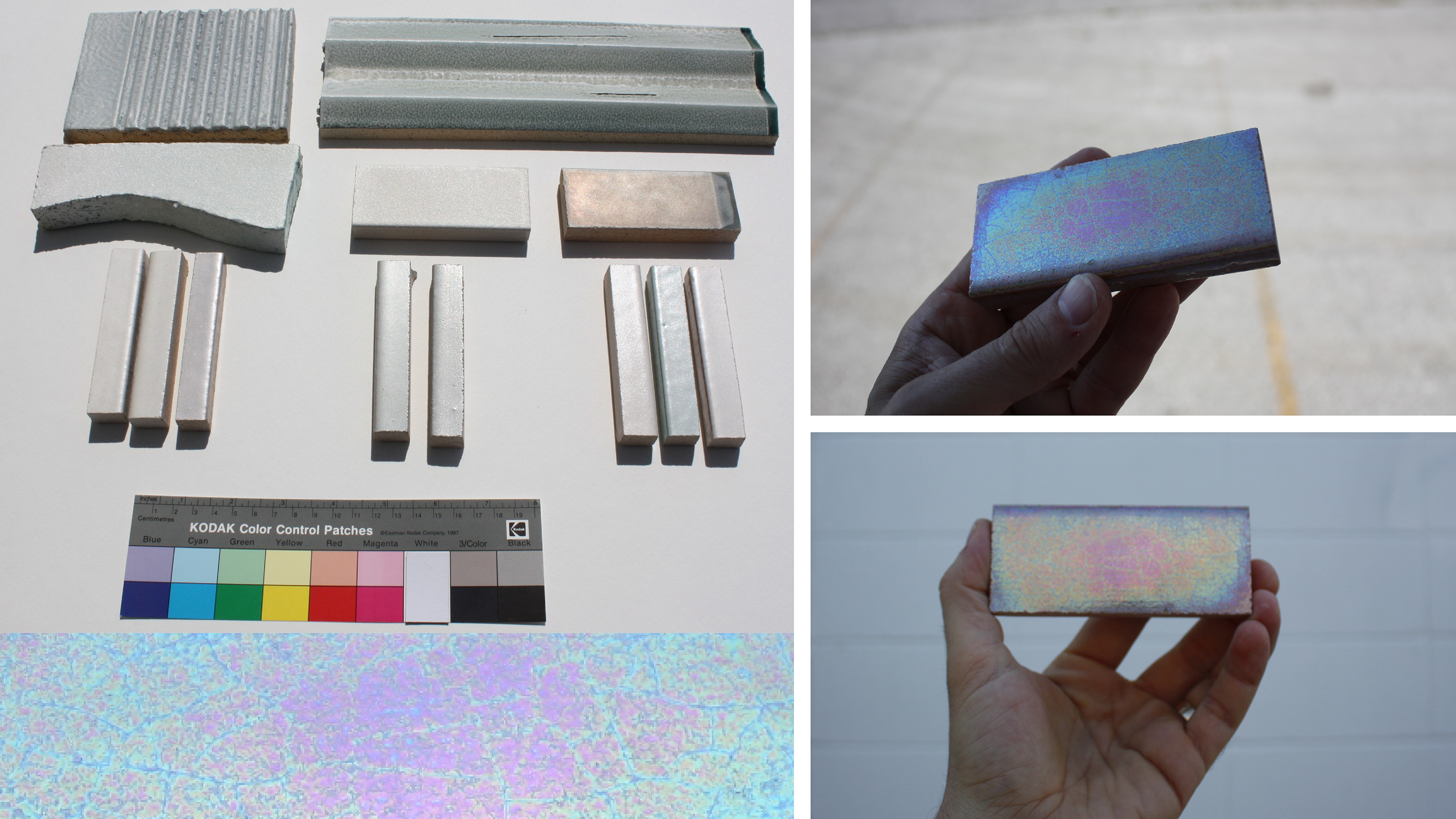
The Matter Factory tested out different glazing options.
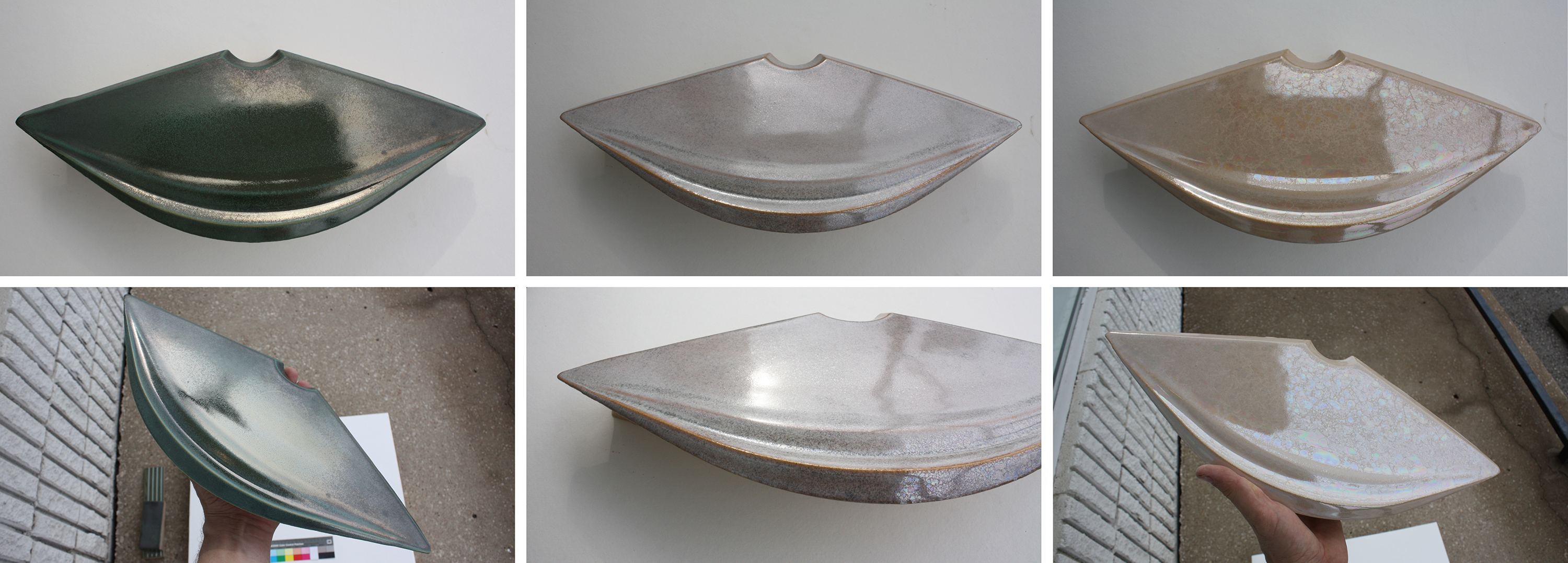
While in its 5th year of hosting the workshop, 2020 was the first year ACAW was virtual.
Once it was decided that the workshop would be held digitally, the next step was to organize a way for viewers to see the work done by all of the participating teams. The final showroom was set up in an Enscape format, with the space designed in a nonagon shape: it consisted of a center space showing each team's project in each category, then branching out into a designated wing for each category.
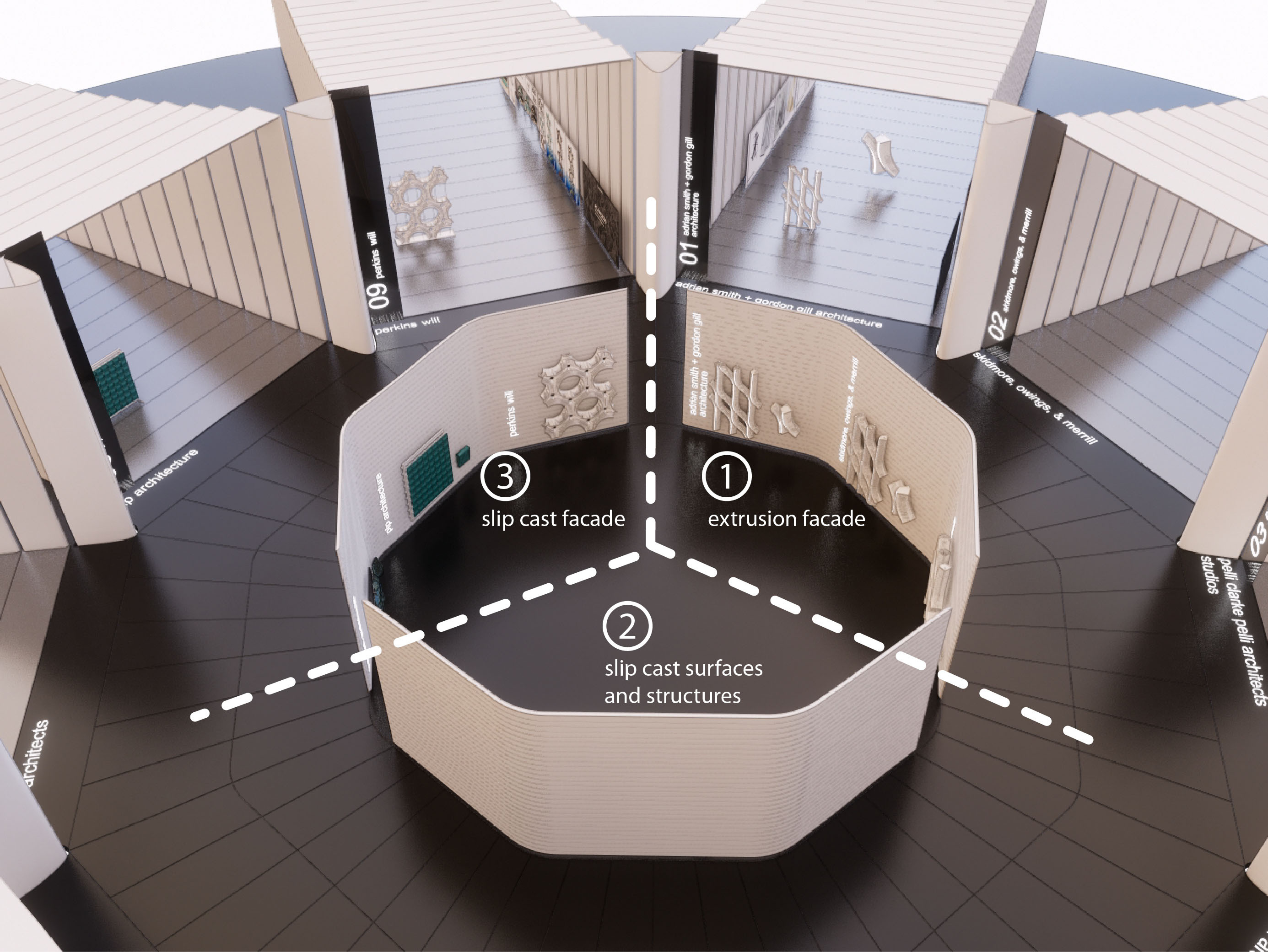
Shown in the images and video below, the Handel Architects space opens with a mock-up of the terracotta system, and as one moves through the space they see examples of early sketches and systems explored, an exploded axon showing the terracotta module with the structural components, concluding with the final designs, glazing studies, and fabrication.
Although different than previous years, the virtual workshop and showroom was accessible to a larger audience than previous years thanks to the accessibility of the virtual format.
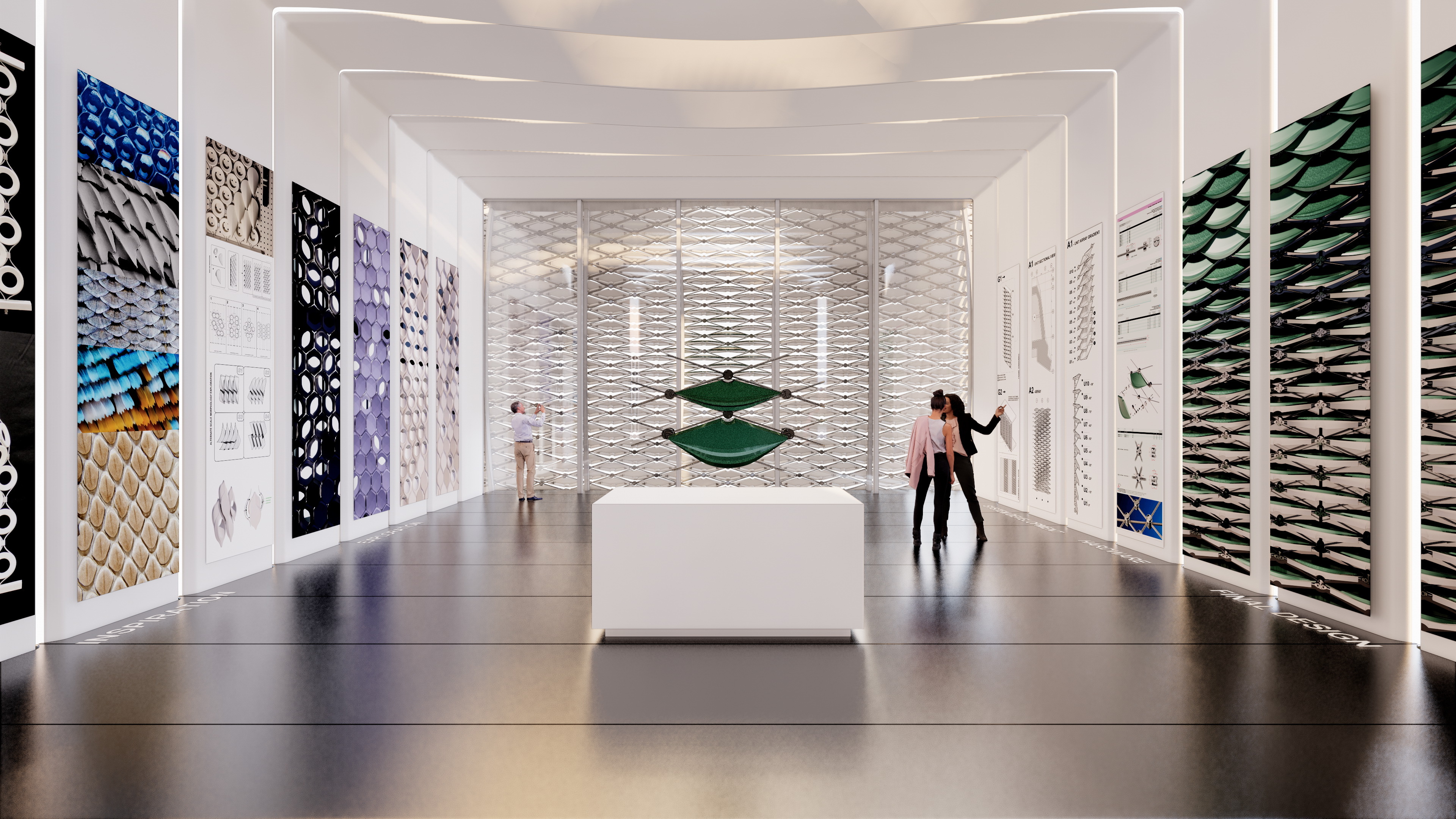
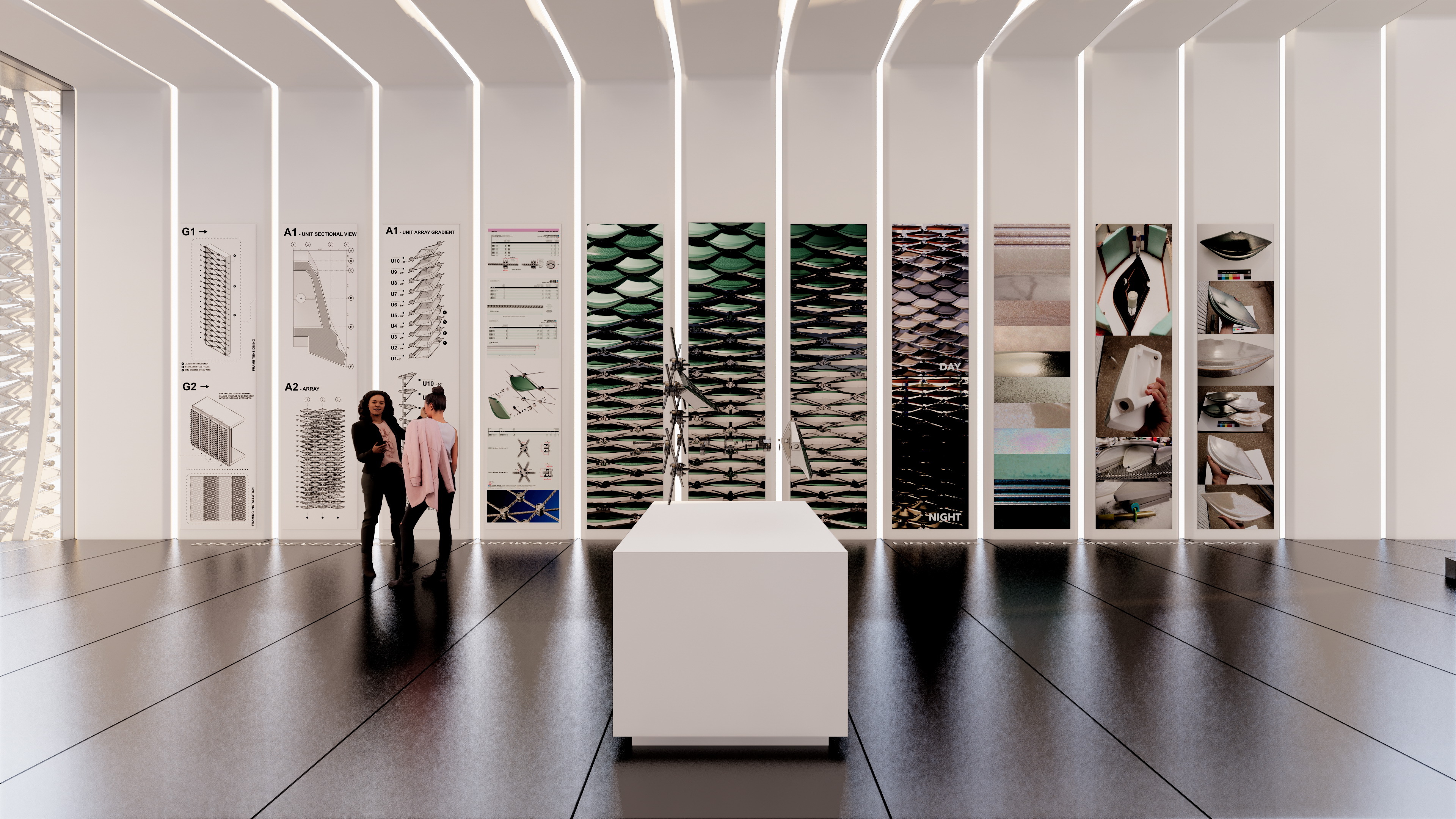