Designing, Detailing, and Building The House at Cornell Tech
"The moral imperative to make big changes is inescapable"
as Al Gore said in An Inconvenient Truth. Our work to create the largest and tallest Passive House building in the world is our answer to this call for change. Though the technology and systems for creating these hyper-energy-efficient buildings had been around since the 1980s, no one had built a project of this scale and density. As the name Passive House indicates, it was originally developed for single-family homes and had been used effectively for low-rise and mid-rise buildings in Europe. But at 26 stories and 352 units of housing, certainly nothing like The House at Cornell Tech had been built before.
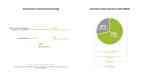
This was a challenge well worth undertaking. Passive House is a game-changer for how all buildings can be designed in the future. Currently the most stringent design protocol for energy efficiency, Passive House is often implemented for projects trying to achieve net-zero energy goals. Passive House structures use an extraordinarily low amount of energy for heating and cooling—60 to 80 percent less than a typical building of a similar size and use. Roughly half the energy used by homes and commercial buildings is devoted to temperature control. Over the course of a building’s lifetime, a Passive House design can dramatically reduce its carbon footprint, while at the same time provide a healthier, more comfortable indoor environment. The House at Cornell Tech is also on track to earn LEED for Homes Midrise v2010 Platinum certification, the highest tier available within the LEED program. A majority of the LEED points derive from the Energy & Atmosphere credit category, where the building is designed to perform 30 percent better than the ASHRAE 90.1 2007 standard.
To design and construct this groundbreaking building, our team researched and oversaw the implementation of a host of new products, procedures, and innovative details. Sketches showing overlapping vapor barriers, tape methods, continuity of insulation, and thermal separation of metals became the new normal for the construction site. Keeping the project on time and on budget required a major coordination effort on our part — communicating Passive House needs and technologies among agencies, contractors, 19 consultants, and 3 clients. In this brief overview, we are sharing some of our strategies and experiences to show a clearer path for those who are contemplating Passive House for their projects.
Taking the Leap
Behind every significant building is a client with a vision. When Cornell won the hotly contested competition to build a tech campus on New York City’s Roosevelt Island, a cornerstone of its proposal was to create the most environmentally sustainable and energy-efficient buildings possible. “There was tremendous ambition in the whole project for sustainability, which was fully consistent with Cornell’s mission to pioneer new technologies,” says Andrew Winters, director of capital projects and planning at Cornell.
It’s worth noting that there was no contractual requirement for the residential tower at Cornell Tech to be Passive House — our client, The Hudson Companies and Related, voluntarily chose to pursue it. Hudson had already built the first Platinum-rated LEED for Homes multifamily mid-rise in 2011, and seriously considered Passive House for an earlier market-rate project. Their experience, combined with Related’s expertise in sustainable design, gave them insight into both green building programs. “Passive House is the real deal,” says Hudson president David Kramer. “A lot of LEED is not that impactful—you get points for being near a subway station, but that doesn’t mean your building is any better.”
Hence, our team was already contemplating Passive House when Cornell issued an RFP in late 2012 for an innovative residential high-rise. Hudson and Related teamed up with our firm, Handel Architects, along with Brooklyn-based builder Monadnock Construction. We had previously worked together on a residential high-rise called Riverwalk Point, close by the new campus. This experience and a deep understanding of residential high-rise design in New York, coupled with our proposal to create an armature of increasing levels of sustainable design features depending on available funding, were key to our selection for the project.
Of course, it was critical that the building be financially feasible to build. For a previous market-rate project, Hudson had calculated that Passive House was too risky. “There’s a risk-return equation when you’re doing things for the first time,” Kramer explains. “We blinked at the last second because we knew we’d be paying a premium in construction costs and didn’t think that we’d be able to get higher rents. And we weren’t sure we could make it up through savings in operating costs.” But for The House at Cornell Tech, the project was structured as a partnership between the university and the developers; Cornell took a significant equity stake in the building to mitigate the developer’s risk and to keep rents affordable for students.
Pushing the Envelope
The basic theory behind a Passive House building is straightforward. They have a heavily insulated, tightly sealed building envelope, combined with energy-efficient mechanical equipment, to dramatically reduce the energy needed for heating, cooling, and ventilation. These three aspects of the building—the envelope, the ventilation system, and the heating and cooling system— were the trickiest to design and construct properly. To minimize cost and complexity in the project, we kept everything else as conventional as possible: The building itself is a cast-in-place concrete structure and has standard materials and finishes for the interiors. It is important to note that Passive House design oftentimes requires only off-the-shelf technology; it is the precise assembly, detailing, and proper selection of systems that is the key to successfully meeting its performance requirements. To create the building’s high-performance skin, we minimized the amount of glazing to 23 percent and designed a highly insulated wall with R-values ranging from R-5 to R-40 for an overall average of R-19. We opted to use a prefabricated metal panel system, with windows inserted and sealed in the shop. The panels had several advantages: cost-effectiveness, better quality control in the factory, and faster on-site construction. In concept, a panelized wall would inherently have fewer joints on the building perimeter than, say, a unitized curtain wall, thus making it easier to achieve airtightness. That was the theory, at least. But the devil was in the details.
“Getting that panelized system to the level of performance we needed was incredibly challenging,” says Lois Arena, director of Passive House services at Steven Winter Associates. “The idea was to create continuous insulation, but in practice there was metal edge meeting metal edge. In retrospect, we would have designed the panels differently, with a thermal break at the end, in order to minimize what had to be done on site.”
Indeed, in Passive House, eliminating thermal bridges—a situation where exposed elements made of metal or concrete conduct heat or cold into/from the interior of a building—was as important as airtightness. In the course of developing the details to meet the rigorous thermal bridging standards, it turned out that a critical component that allowed the building to function as designed was a little piece of plastic, specifically engineered by the exterior wall contractor, which thermally separated the outer layer of the façade from the interior.
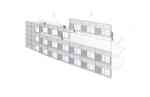
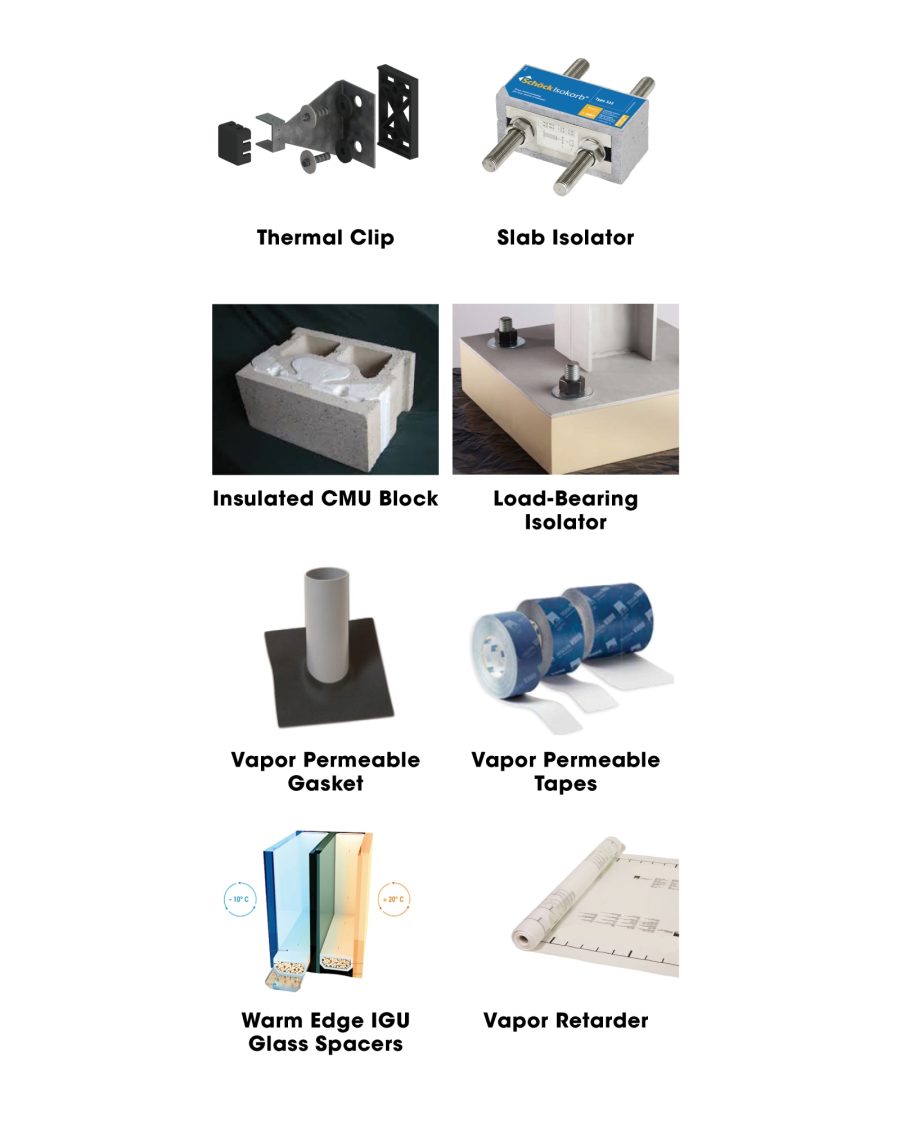
Many off-the-shelf products are available to mitigate thermal bridging and air infiltration.
Staying Within the Energy Budget
Unique among sustainable building programs, Passive House has an absolute threshold on how much energy a building can use per square foot, not just for cooling and heating but also for the whole building. This includes power to run equipment, lighting, elevators, and appliances. This limit makes the program incredibly effective at reducing energy use, since the building has to be intrinsically efficient—it’s not possible, for example, to install a slew of fans to circulate air or a cluster of pumps to circulate water and still meet the energy budget. Some potential solutions had to be rejected out of hand because they required too much power. “The building design was like a sculpture that was constantly being molded based on Passive House criteria and calculations,” says Alan Hajtler, Hudson’s director of construction. The density of the building—one person per 550 square feet—compounded this challenge. “We had a constant battle with the total energy budget,” says Arena. “The more people per square foot, the harder it is.” (Currently, Passive House does not take into account differences in building usage or number of occupants.)
It took the team months to resolve which ventilation and heating/cooling system would be optimal for this project. In Passive House, an energy recovery ventilator (ERV) extracts hot and cold energy from the exhaust air and uses it to treat the fresh supply air. But how to get the air to and from each space in a building this big without busting the energy budget was a major challenge.
One option, found often in smaller PH buildings, was to install individual ERV’s within each apartment allowing for a self contained ventilation system. We determined that such a “unitized” approach would cost an additional $1.5 million due to increased building height and horizontal ductwork. Also it quickly became clear that the maintenance for 352 small ERV’s was going to be quite a burden on the building management.
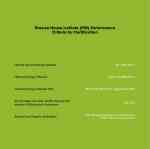
Passive House sets a maximum threshold for both total overall energy use, as well as caps for heat, cooling, and air infiltration. The overall savings in energy use can be substantial: 60 to 80 percent less than conventional construction.
Our team decided upon the alternative: a “centralized” system. In this instance, each apartment has vertical supply and exhaust shafts that provide a pathway for air to travel to one of two energy recovery ventilators that sit on the building’s rooftop. Finding ERV’s large enough and suitable for this project was a challenge. The initial concept envisioned four ERV’s, but these were costly, space-intensive and strained the energy budget. Through resourcefulness of Related’s team, we were able to procure two customized large units to meet the project’s ventilation needs.
For heating and cooling, we opted for a low-energy variable refrigerant flow (VRF) system. Condensers that treat the refrigerant for heating and cooling sit on a thermally broken balcony off the side of the building, and each condenser pushes refrigerant to two half-floors for greater efficiency (floors on the north might need heating while those the south might need cooling). Our engineers at Buro Happold, together with Luke Falk, head of Strategy and Product at Related, determined that with such a high-performance wall and relatively small space to condition in each apartment, the individual evaporators needed only to have a quarter-ton capacity. However, there was nothing on the market with less than a one-ton cooling capacity. Despite the quantity involved (over 500 evaporators), the available suppliers were not prepared to provide a customized unit. We hope the market will respond with smaller capacity units in the near future.
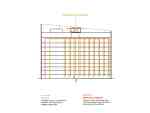
Many Passive House projects in the US and Europe employ “through-wall” ERVs, which take up very little space and provide the ventilation system for an apartment or home. However, each unit requires an air filter that needs to be changed regularly. In a 26-story high-rise, with more than 500 occupants and irregular tenancies, the maintenance costs for changing that many individual filters would have been prohibitive.
The central air distribution system at The House at Cornell Tech has only a small number of air filters in the rooftop ERVs: easy to maintain without disturbing tenants.
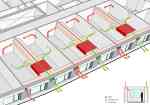
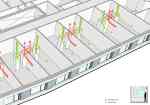
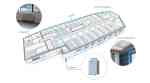
Getting the Go-Ahead
Obtaining city approvals for the building was definitely more complicated than for a regular project. There were technical issues where the requirements for Passive House and the city building code came into conflict. In one instance, the amount of ventilation required by code, Passive House, LEED, and Energy Star were all different and had to be reconciled. “There’s an argument to be made that over-ventilation is bad, since it results in extremely dry air, and you can’t meet your energy budget if you are constantly heating and cooling so much air,” says Arena. Fortunately, although Passive House called for a lower continuous flow rate due to the tightness of the building, it had a higher air-change rate per hour, meeting the intent of the code if not the letter.
But the larger hurdle was getting through a public design review process, a condition for all projects at Cornell Tech, which is located on city-owned land. The city’s Public Design Commission felt that the building should have an all-glass façade, based on a pre-disposition that it should be more transparent. “Getting the design commission on board for something that deviated from the standard playbook for a Manhattan apartment building was the most challenging part of the process,” says Winters. “Those are not the easiest conversations to have.” We had to explain how the wall needed to be mostly opaque to meet Passive House requirements, and that a façade with deep extrusions or indentations would be less efficient. The PDC eventually endorsed our position, both on aesthetics and the underlying sustainable design mission.
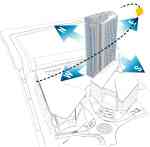
The site location and orientation were particularly advantageous to meeting Passive House goals. The compact shape, with minimal east/west exposures, when combined with oblique angles at corners were conducive to passive control of thermal transmission.
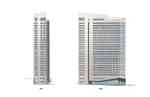
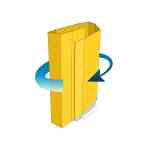
To meet Passive House requirements, we had to create a thick insulated wall that encompassed the full height of the building. Our façade concept, which we dubbed “The Wrap,” is a continuous plane that wraps around the building and is bent at multiple locations to reduce the boxiness of the tower. It is cut open only in two locations: vertically at the condenser balconies, to draw the eye towards the front entrance; and horizontally, at the ground-level lobby overlook we call “The Porch.”
Fixing Things on the Fly
Going into the project, we knew that even if the design worked perfectly on paper, there were so many unknowns that could come up during construction. While we tried to work out everything ahead of time, many of the details that were planned in preconstruction ended up being changed onsite. “No matter how hard the design team works on developing details early on, it's very hard to encompass all conditions to accomplish an airtight building,” says Louis Schwartz, senior project superintendent at Brooklyn-based Monadnock Construction. “You really need to get the trades involved, the people who are actually doing the work, and educate and train them.” Ryan Lobello, our associate in charge of construction administration, worked closely with Vidaris, our façade consultant, SWA, and Monadnock to carefully custom tailor each of myriad details involved.
Monadnock’s construction management team went to extra lengths to understand Passive House. The entire team went through rigorous Passive House contractor certification training, which culminated in building a 10-by-20-foot mockup that had a window and a door as part of a blower door test. “It met the Passive House standard, but we could see that every pinhole was leaking smoke,” says Aleksandr Yelizarov, vice president and project executive at Monadnock Construction.
One of the key challenges was to make the building airtight working with a construction crew that was used to building high-rises a certain way. Maintaining the integrity of the vapor barrier is critical in Passive House; instead of caulking, tape is used to seal the openings for windows and other details. “The number of times I heard, ‘That’s not normally how we do things’ was exponential,” says Arena. Monadnock pre-emptively hired a consultant to train all the subcontractors on how to apply the tape properly.
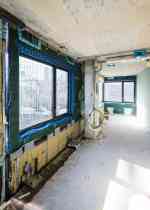
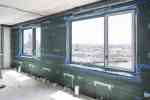
The advantages of the panel system were factory quality control, speed of delivery, and fewer exterior joints to be sealed. But each panel had to be seated on the floor slab, and each connection point needed to be sealed at the air barrier. There are more than 123 supports per floor, and more than 3,000 on the entire building. Our initial strategy was to create self-sealing flaps attached to the panel in the factory, then applied in the field. This proved to be less efficient than installing the lower half of the barrier in the field, with individual patches at each panel clip.
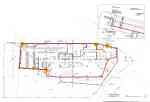
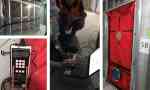
The firm also set up rules for the construction site, warning against leaning building materials against walls and reminding crews to alert a supervisor immediately of any accidental punctures of the airtight barrier. “We told them that they weren’t going to Passive House prison, but how important it was to let someone know if they made a mistake so we could repair it,” says Schwartz.
The construction team led by Yelizarov also came up with a fix for a major crisis that threatened to derail the schedule. After the first ten floors had already gone up, the factory-installed vapor barrier started to detach from the panels. To keep the project on schedule, the contractor developed a procedure for reinstalling new vapor barrier to the panels on site. The team also discovered efficiencies and solved installation problems as the panels were erected, yielding a super-tight building that heroically passed Passive House’s notably difficult blower-door test, with results that were four times better than required.
Finish Line
The building finished construction in June 2017, ahead of schedule and within budget. On July 20, the entire team celebrated on the rooftop. “It felt great—it was quiet and comfortable, even though we probably had more people than it was rated for,” says Arena. Over the last three years, The House at Cornell Tech has drawn much attention from builders, other educational institutions, and municipalities both local and overseas. It has been an important catalyst for change, both as a paradigm for creating dramatic energy efficiency as well as opening minds to the efficacy of Passive House when scaled up to this size and height.
Indeed, the Passive House protocol is being incorporated into significant private and public projects around New York City. Earlier this year, Handel Architects was part of the team designated by the Department of Housing and Preservation to deliver the first 100-percent affordable housing project requiring Passive House certification for a City sponsored competition. Currently in design, we expect this East Harlem development to show that substantial energy efficiency and affordability can be converging objectives. We expect this project to further advance the idea that Passive House can and should be commonplace in buildings regardless of their use or size.
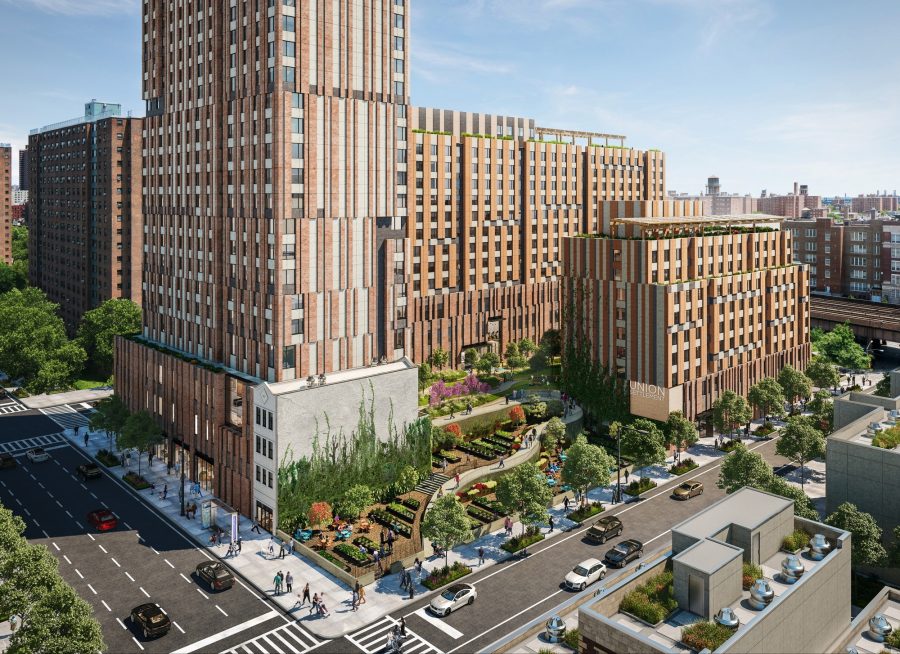
Looking forward
Sendero Verde in East Harlem is a three building, 760,000 SF complex with 650 affordable apartments all designed to Passive House criteria. Now under construction, it will be the largest fully affordable Passive House building in the world.
The House is a groundbreaking example of sustainable architecture - the largest and tallest Passive House building in the world.
For the entire team, this project has been a successful beta test to meet our moral imperative to minimize the carbon footprint of buildings. It’s our answer to the call for making big and meaningful change to combat global warming.