Sustainability Report: Passive House Facade Design and Construction
Sustainability Standards in a Time of Climate Crisis
In May of 2019, the Anthropocene Working Group voted to designate a new geologic epoch, the Anthropocene, an era in which people have become a major geological force (Subramanian, 2019). Human civilizations have reconfigured the Earth’s surface and the atmosphere around it. A week before the vote, fossil fuel emissions drove atmospheric carbon dioxide levels to 415 ppm for the first time in 3 million years (Harvey, 2019). Our planet is in crisis (and humans are undeniably responsible) but recognizing humanity as a force of nature also brings hope that our capacity for rehabilitation can equal that of destruction. Humans have shaped our present, it is our responsibility to positively shape our future.
To mitigate the impact of this climate crisis, the United Nations’ International Panel on Climate Change (IPCC) has stated we must limit future global warming to 1.5 deg C [2.6 deg F] above 2015 temperatures. Models show that by 2030 global net anthropogenic CO2 emissions must decline by 45% from 2010 levels and reach net zero around 2050 (Allen et al., 2018). In the United States, CO2-emitting fossil fuels account for 63.5% of energy generation (EIA, 2018). With buildings using roughly 40% of the global Primary Energy Consumption, architects, developers, engineers, and the whole construction industry bear much responsibility in reducing fossil fuel consumption (GlobalABC, 2018). Growing populations and higher standards of living are increasing pressure on the built environment and it is critical that architects design buildings to maximize efficiency without sacrificing flexibility and occupant comfort.
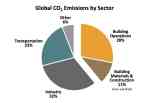
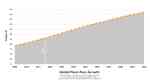
Prescriptive Standards for Complex Buildings
As building standards become more complex, it is increasingly difficult to have a holistic impact with prescriptive code requirements.
In the last three decades, governments have begun regulating energy consumption using energy codes and incentive programs. These tools have made an impact but “there has also been growing sentiment that energy codes in their current form are getting too complex, change too often, limit design flexibility, don’t achieve their desired outcomes… and do not consider the building as an integrated system.” (Rosenberg, 2019). Many of these perceived shortcomings stem from the US energy codes reliance on prescriptive measures that set requirements for individual building components (Rosenberg, 2019). For example, the 2016 New York City Energy Conservation Code (NYCECC), requires R-30 roof assemblies and limits glazing SHGC to a maximum of 0.4 (NYC Buildings, 2016). The result is a focus on component performance and not whole-building energy efficiency. As buildings systems become more complex it is increasingly difficult to account for all applicable components and the impact they have on each other. The result is multiple compliant buildings with very different equivalent energy performance and no universal metric for comparison (Rosenberg, 2019).
Since its inception, the International Energy Conservation Code (IECC), the foundation for most US energy codes, has offered an equivalent predictive performance pathway as an alternate to the prescriptive compliance method (ICC, 2018). This pathway establishes a baseline and allows building components to perform better or worse than code if the cumulative result exceeds the baseline. The advantage being “predictive performance allows for a compliant design solution that is more flexible than prescriptive solutions and can be optimized for particular building’s climate, operations, system interactions, and utility rate structure” (Rosenberg, 2019). Despite providing increased flexibility, the target baseline is still an equivalent to a prescriptive code. This presents a problem because prescriptive codes have been shown to produce inconsistent levels of energy use meaning the performance equivalents are biased toward the more lenient end of the spectrum (Rosenberg, 2019).
The Impact of Sustainability Standards
Standards that focus on individual components without looking at whole-building performance allow pathways to compliance without addressing the most urgent aspect of Earth's climate crisis: the reduction of Greenhouse Gas emissions.
To go beyond energy codes, the building industry has developed voluntary sustainability standards. The most prolific in the U.S. is the U.S. Green building Council’s (USGBC) Leadership in Energy and Environmental Design (LEED) standard. To achieve LEED certification a building accumulates points from a diverse group of categories. Historically, this was a largely prescriptive standard that created equivalencies between a variety of credits with very different impacts on the overall energy use of the building and its occupants. However, LEED v4 has put greater emphasis on predictive performance modeling and energy efficiency including credits for achieving Passive House certification. These performance-based compliance pathways offer greater flexibility, but prescriptive pathways still exist as an alternate (USGBC, 2019). This legacy of prescriptive standards presents the same challenges as U.S. energy codes. Its performance is relative to a baseline established by a prescriptive standard, in this case the respective version of ASHRAE 90.1(USGBC, 2019).
These standards have been critical in pushing the industry toward more sustainable building practices, but in their current form they will not restrict energy use enough to reduce emissions at the pace required to meet the IPCC’s targets (Allen et al., 2018). By basing compliance on individual components rather than holistic whole building performance, these regulations provide pathways to compliance that avoid the most urgent aspect of Earth’s climate crisis, the reduction of greenhouse gas emissions (Rosenberg, 2019). One solution being explored by policy makers is to set context-specific baselines based on whole-building source energy use intensity (EUI). EUI is favored because it is closely tied to emissions and greenhouse gas reduction and tracked in other existing standards and regulations (Rosenberg, 2019). Using holistic and universal baselines will result in standards that prioritize energy efficiency and emissions reduction without compromising design flexibility or inhibiting innovation. The Passive House (PH) standard is a testament to the success whole-building predictive performance-based standards can have in increasing energy efficiency and promoting innovation. This is exemplified in the subsequent case studies.
The Passive House Standard
Focusing on measurable performance metrics while maintaining design flexibility.
The PH standard establishes performance criteria for the entire building, including maximum allowable values for source Energy Use Intensity (EUI), heating demand, and cooling demand, while maintaining strict requirements for air tightness, ventilation, and thermal comfort (PHI, 2019). By focusing on measurable performance, a design team has the flexibility to respond to a project’s unique context and client requirements. Unlike the pass/fail nature of prescriptive standards, energy efficient design decisions in one area are rewarded by increasing the allowable energy budget to be used in other more challenging parts of the project. The PH criteria establish variables that can be manipulated to create a unique project without sacrificing energy performance.
PH design solutions result in continuously insulated and tightly sealed building envelopes which when combined with energy efficient mechanical equipment have been proven to dramatically reduce the energy needed for heating, cooling, and ventilation in moderately sized buildings for decades (PHI, 2019). Over the last ten years, architects and consultants in cities around the world have been working to scale-up this standard for applications where the impact is greatly magnified. Handel Architects is designing and constructing some of the largest and tallest Passive House buildings in the world (Passive House Database, 2019). Examples of which have been outlined in two case studies:
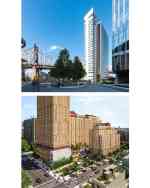
The House at Cornell Tech
Completed in 2017 on Roosevelt Island in NYC, is a 352-unit residential tower for graduate students and faculty. The tower is clad with a prefabricated panelized aluminum facade with triple glazed punched windows and double-glazed storefront. The building was certified by Passive House International (PHI) and was the tallest and largest certified Passive House in the world when completed.
Sendero Verde
A multi-phased mixed-use development with three buildings and over 700 units of affordable housing in East Harlem, New York. Primary façade types include hand-laid brick cavity wall and EIFS. The project is currently under construction.
What is Passive House?
Passive House (PH) is a building concept, not a proprietary system and a focus on performance and user comfort was part of the standard since its inception. The first Passive House, “Darmstadt House” was completed in 1991 near Frankfurt, Germany by Wolfgang Feist. It was provided with “a highly precise data measurement and acquisition system to examine the achievements of the project’s objectives” (Passive House Academy 2017, 12). This eventually evolved into the PH standard for whole-building energy modeling and verification used today by the Passive House Institute (PHI). PHI is the organization certifying Passive House buildings and they have been researching and applying the PH standard to projects in various climate types around the world. (Note: the Passive House Institute United States (PHIUS) is an alternative certifying entity that uses slightly different criteria, this paper focuses on the PH standard as set by PHI, the certifying body for both case studies).
PHI establishes the performance criteria based on a project’s program, climate zone, and geographic location. The certified result is a project with a 50%-80% reduction in energy usage compared to a conventional building (Passive House Academy 2017, 12). While every project is unique, the guiding principles remain the same: to provide a comfortable and healthy interior environment without exceeding a maximum Source Energy Use Intensity (EUI) and heating/cooling demand by combining a tightly-sealed envelope with efficient MEP systems with continuous ventilation and heat recovery.
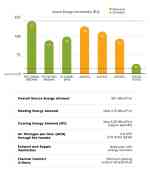
Criteria for Certification
The case studies exemplify these principles while contributing new ideas toward the design and development of Passive House buildings, specifically in high-rise and multi-use applications. Both projects are in New York City with a primary building occupancy of R-2 (multi-family residential). As such, both projects must meet the criteria to the right for certification.
These criteria illustrate how ambitious the PH standard truly is. The estimated Source EUI for a building following the 2018 IECC is 144 kBtu/sf/yr (NYSERDA, 2017). A PH certified building is nearly 4 times better at 38.1 kBtu/sf/yr. Even with the 45% reduction required by the IPCC by 2030, a standard building will have almost double the EUI of a Passive House building built in 2019
Passive House and Design Flexibility
Passive House buildings are energy efficient but how does this standard impact the design of a building?
It stands to reason that such stringent performance requirements could restrict the flexibility of a project to respond to specific design conditions. This is where the PH energy model plays a big role. By modeling every building component, the design team can experiment with how different variables impact building performance. Variables can be manipulated to meet specific project requirements allowing for a give and take between the individual building components resulting in a unique design that meets identical performance criteria, as is illustrated in the two case studies. The full project teams (architect, ownership, consultants, and contractors) meet specific demands by finding the right balance of the following variables:
- Site and Program (form factor, orientation, daylighting/shading, urban context, aesthetics)
- Exterior wall
- Air Sealing
- Window Performance
- Thermal Bridge Mitigation
- Mechanical System
These are just some of the many variables considered. The PH standard’s data-driven approach sparks innovation and allows each new project to find its own path. Through knowledge-sharing and increasing industry familiarity with the PH requirements and techniques, more variables are discovered, and the standard becomes more flexible and achievable. In each case study the design team had ongoing conversations with PHI to analyze and solve the unique challenges posed by high-rise applications, a relatively new application for the PH standard.
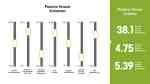
Passive House Implementation
The first case study, The House at Cornell Tech, has drawn much attention from builders, educational institutions, and municipalities both local and overseas. It has been an important exemplar of the feasibility of dramatic energy use reductions and the efficacy of Passive House at the scale of New York’s high-rise residential buildings (Hurley, 2019). The success of this project led to the second case study, Sendero Verde. The NYC Department of Housing Preservation Development (HPD) organized the SustaiNYC competition as the first city sponsored RFP requiring PH certification (NYC HPD, 2019). Handel Architects was part of the winning team designated to deliver the 100% affordable housing project to PH standard. The project has drawn the attention of organizations such as the NY Department of City Planning, New York State Energy Research & Development Authority (NYSERDA), and the Building Energy Exchange (BEEX) (SV Project Presentations, 2018-2019).
While the standard has verified success at smaller scales, there were several challenges to address at this large scale. At the macro-level PH continues to face the challenges common among all EUI target-based performance standards. The first of which is setting appropriate and achievable targets, the most critical being the maximum source EUI (Rosenberg, 2019). Historically, this target is determined exclusively by climate zone and occupancy type. Both The House and Sendero Verde were designed to meet the 38.1 kBtu/sf/yr required for multi-family residential in New York’s climate zone 4. This target was originally established for smaller buildings with fewer occupants/SF and large-scale PH buildings being built around the world have struggled to meet these stringent EUI targets (specifically very dense buildings like student and senior housing). To acknowledge the benefits of increased density and set more achievable EUI targets, PHI has recently introduced a density tool that modifies the EUI target based on the occupants/SF
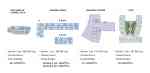
Energy Modeling and Field Verification
Rigorous on-site protocols and data collection turn predictive performance models into real energy savings.
The second macro challenge faced by PH in large-scale buildings is the reliable prediction of building energy use. To this end, PHI uses a robust energy modeling tool called the Passive House Planning Package (PHPP). All envelope conditions and thermal bridges are modeled, as are MEP systems, site conditions, and projected user plug loads. This tool identifies the variables that can have the greatest influence on the building’s final energy use and predicts how a design will meet the required PH criteria.
Verification of these predictive modeling tools is essential to any predictive performance standard. PHI utilizes a robust testing, verification, and commissioning structure (PHI, 2019). Inspection and testing occur throughout construction with critical details verified in photos, checklists, and product data. These protocols set the PH standard apart from other performance targets. For example, NYCECC requires a building envelope to maintain an airtightness of 3 ACH at 50 pascals of pressure, but there is no compliance method to verify that this airtightness was achieved (NYCECC, 2016). For a PH to become certified, it must prove it has met the much more stringent 0.6 ACH at 50 pascals by employing a whole-building blower door test. This is a non-negotiable requirement for certification.
After construction is complete and certification achieved, there are requirements for post-occupancy commissioning and performance analysis to confirm the building is performing as modeled (PHI, 2019). Unlike the on-site blower door test, it may take several years to get an accurate picture of how the certified project is performing. Since large-scale Passive House projects have just started coming online in the last few years there is accumulating data confirming that the overall building energy use is meeting pre-construction predictions for the mechanical and façade performance. User plug loads have been underestimated and PHI is continuously updating the density EUI targets to more accurately predict user energy use. Beyond verifying performance, data collection and analysis requirements during construction and post-occupancy give the project team valuable insight into which strategies are most effective and should be implemented in future projects.
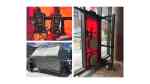
Room for Growth
Existing shortcomings in the Passive House standard leave room for expansion and collaboration.
While there is much to be celebrated about the growing popularity of Passive House. It is important to recognize that there are still opportunities for improvement, including:
- Accounting for the embodied energy of materials and methods used to construct the building when analyzing whole building energy use and performance.
- Accounting for the management of manufacturing and construction waste streams.
- Accounting for the sourcing and chemical composition of materials. Passive House’s focus on interior health and comfort is based around thermal performance, humidity, and ventilation. There is no requirement regarding other building health concerns such as VOCs and off-gassing which are vital to maintaining healthy interior environments in an air-sealed building.
It is these areas where prescriptive codes and points-based systems can offer supplemental benefits. To further limit greenhouse gas emissions, design teams should combine the whole building energy concepts of Passive House with the embodied energy, waste stream management, and material safety requirements of systems like LEED v4.0, WELL, or Declare.
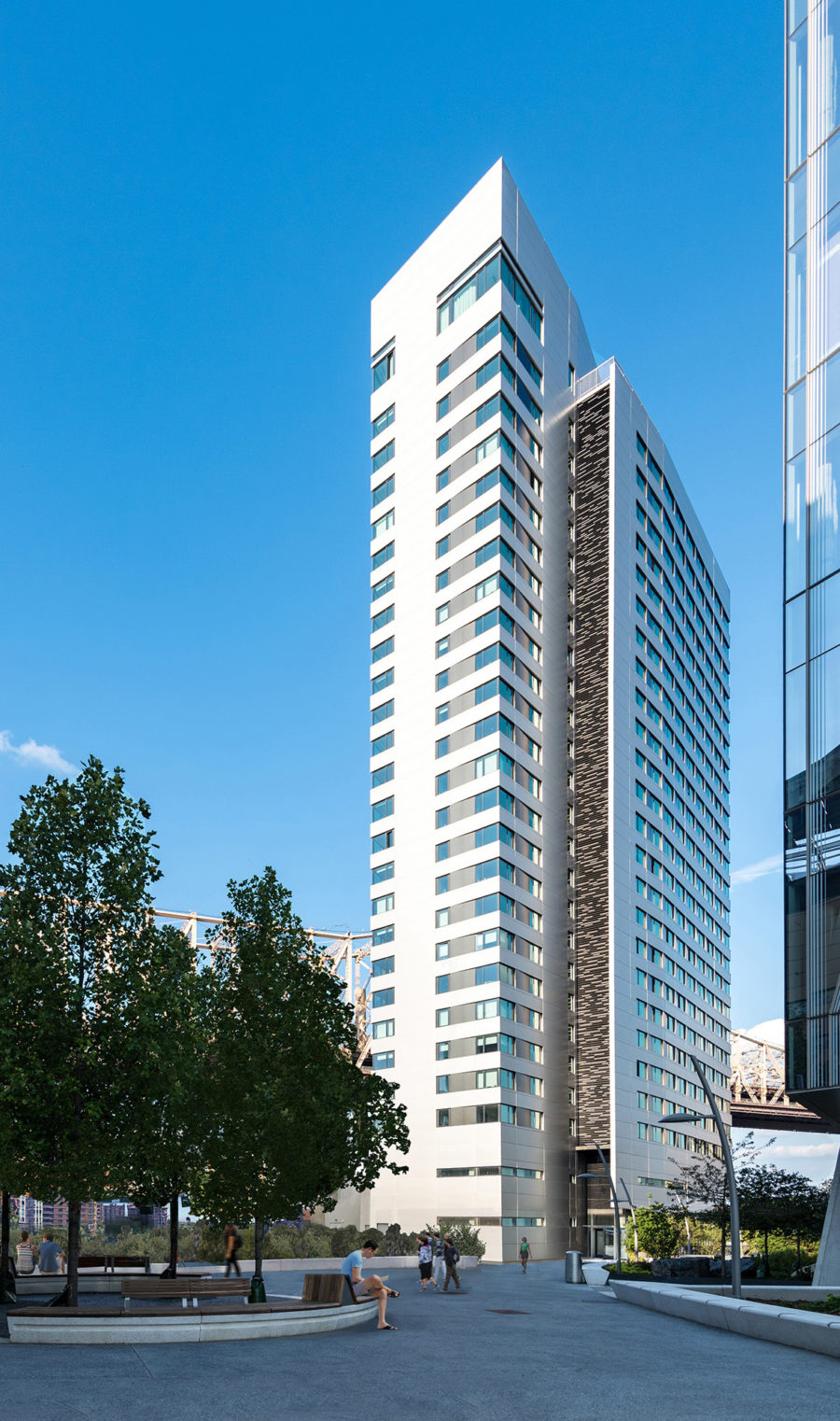
Case Study 1:
The House at Cornell Tech
The House is part of Cornell Tech's new 2.1 million square foot technology campus on Roosevelt Island in New York City. The 272,000gsf building is designed to reinforce the unique model of academic integration, multi-disciplinary research, and collaboration at the core of the Cornell Tech mission.
Its 352 residential units, 500 beds, and ample amenity spaces serve as a lively and comfortable living place for informal social interactions between students and faculty residing on campus. To meet the campus’s requirement for sustainable design, the building’s developers, The Hudson Companies and Related Development, chose to pursue Passive House. The House was constructed by Monadnock Construction and completed in 2017, when it became the largest and tallest residential building in the world built to Passive House standards (Gray, 2018). To complete this unprecedented feat, the design team creatively took advantage of the flexibility afforded by this performance-based standard to address the myriad challenges outlined within this case study.
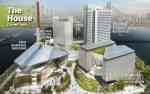
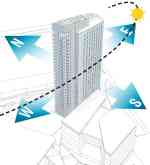
Site and Program
As the tallest building on campus, The House acts as a campanile to identify the new campus to observers from Manhattan and Queens. The open brownfield site allowed the master plan team at SOM to optimize the building’s orientation to take advantage of year-round direct solar exposure and allowed Handel Architects to optimize it’s massing for Passive House performance. The long axis is oriented East to West and the longest exposures face due North and South. The result is two HVAC zones maximized for North and South exposures and limiting East and West. This orientation also reinforces the concept of the campanile, by presenting the slender proportions to the neighboring boroughs on either side of the East River.
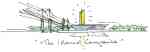
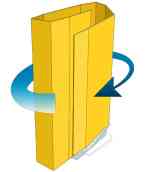
Massing
Sharp corners were eliminated from the massing, as these conditions produce thermal bridges by increasing the amount of exposed facade. Instead, the facade was developed as a series of folded planes that wrap the building like a thermal blanket opening in a reveal extending the entire height of the building. This reveal is designed to be the building’s “gills”, providing an enclosed, screened exterior space for heating and cooling condensers, allowing the building systems to breathe
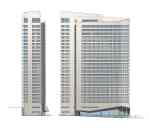
A Residential High-Rise Aesthetic
The project is located on city-owned land and was required to receive approval from the city’s Public Design Commission. The Commission felt that the building should have an all-glass façade, based on a pre-disposition that residential buildings should be more transparent. Existing notions on what a “typical building” should look like are a common challenge for PH designers to overcome. The design team explained that - to meet Passive House requirements glazing areas needed to be carefully calibrated, and that an all glass façade was simply too expensive. The PDC ultimately endorsed the project, both on aesthetics and the underlying sustainable design mission
By optimizing glazing to suit room size as well as Passive House requirements, and manipulating the massing and orientation, the design team used the site variables to start the project on a solid foundation. This allowed increased flexibility in addressing challenges at the detail and systems levels to meet the performance criteria while keeping the project on budget. Façade, ventilation, and HVAC systems were required to be state-of-the-art, but everything else was kept as typical to the NYC rental market as possible: the building is a cast-in-place concrete structure and has standard materials, appliances, and finishes for the interiors.
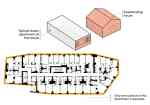
Surface to Volume Ratio
High-rise typologies have one big advantage over smaller PH buildings. A typical home has five exterior surfaces from which to lose heat (roof and four walls), but an apartment often has only one facade exposure. This ratio of exterior surface (S) to conditioned volume (V) determines a building’s compactness. In a compact building with a low S/V ratio the same efficiency can be achieved with lower envelope performance requirements. This is further improved by the high number of occupants per façade area resulting in high internal gains which are captured by the airtight enclosure and relieve pressure on the mechanical systems. These were known advantages from the project genesis, but to fully understand its impact the design team had to consider several exterior wall variables including air-tightness, thermal bridging, window performance, constructibility, and market limitations.

Exterior Wall Construction
For the exterior wall construction, the design team selected a prefabricated mega-panel system which provided several advantages: cost-effectiveness, quality control in the factory, and faster on-site construction. The panels were hung from floor slabs like a conventional curtain wall assembly. At roughly 10 feet tall by 30 feet long with the ability to turn corners, the mega-panel system has far fewer joints than a unitized curtain wall making it easier to achieve airtightness. Eastern Exterior Wall Systems was selected to fabricate and install the façade at an early stage to aid in the design and detailing of the system. The completed panels were shipped to the island on a barge and the entire façade was erected in only 8 weeks enclosing the interior environment and allowing for expedited starts to interior finishes and significant time savings.
To reinforce the campanile concept, the exterior “Reynobond” aluminum composite material rainscreen cladding received PPG’s Duranar multi-coat coil-formed polychromatic coating that reflects light and naturally shifts from a bright silver to a warm champagne. The coating system is also engineered to meet EnergyStar solar reflectance limits and reduce solar heat gain on the façade (PPG Industries, 2009). The ACM cladding is attached to the backup wall on thermally-broken supports with 2-5 inches of continuous mineral wool insulation in the cavity. The backup wall is 6-inch heavy gauge steel studs infilled with 6 inches of mineral wool insulation and exterior grade sheathing covered in a continuous vapor-permeable air barrier (“exterior AVB”). The interior side of the panel was covered in a second “smart” air barrier that remained exposed during installation (“interior AVB”). Windows were installed and sealed in the shop. The result is a continuous, highly-insulated enclosure with R-values ranging from R-5 at the panel joints to R-40 for an overall de-rated average of R-19.
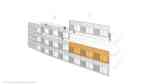
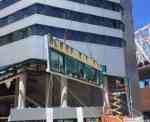
Air Sealing Strategy
An average building in New York City loses a tremendous amount of energy from infiltration through leaky exterior walls. To meet Passive House requirements, The House would be limited to the PH requirement of 0.6 ACH. Once the building was fully enclosed a blower door test is performed and if the building does not reach that target, certification is denied. This meant that the design, analysis, and construction of every detail mattered greatly to the overall success of the project.
The panel joints impact several variables in the PH model, but they also have a critical impact on construction sequence. These mega-panel systems often use dry-gasketed joints to provide an immediate seal at installation, but at a significant cost premium. To reduce cost the team opted for wet sealant joint; a joint that requires caulking from the outside after the entire façade was installed. This posed a challenge to verifying that the ongoing installation of the façade would ultimately yield an airtight condition. To overcome this challenge, the design team incorporated a continuous interior AVB which allowed the contractors to seal the enclosure from the inside on each floor and perform intermittent, localized testing. This decision impacted the interior floor area as the team was required to set the perimeter columns 8 inches back from the edge of slab to provide enough clearance for a person to get their hand between column and wall and install an effective seal.
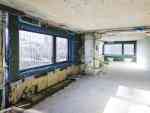
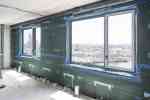
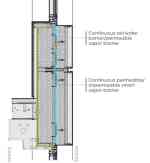
The Airtight Layer
For this reason, the interior AVB is considered the “air-tight layer”, the point from which the building is completely sealed. This approach allows the construction and inspections team direct access to the air-tight layer to investigate issues during testing without impacting the exterior facade. It also provides superior vapor transmission control. PH requires that wall assemblies be modeled in THERM to determine localized dew points and identify areas of potential condensation. The exterior AVB is inside the panel assembly with insulation on its warm side as well as the cool side. Studies showed that if moisture penetrated the interior insulation from the inside of a unit under the right conditions, there was a high potential for condensation on the interior side of the exterior AVB. To combat this, the team used a Pro Clima Intesana “smart barrier” for the interior AVB.
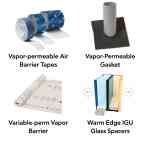
Specialized Products
Smart barriers have pores on a molecular level that open under certain humidity conditions to become vapor permeable when you want vapor to escape into the exterior wall and transition to vapor impermeable when you don’t.
The smart barrier is one of several specialized products used at The House to maintain a continuous air seal. Air barrier tapes were used to seal window frames to the adjacent air barrier and pipe and conduit penetrations were fitted with vapor-permeable gaskets with continuous tape around the perimeter. These products allow the contractors to ensure a continuous air seal with consistent and easily verifiable protocols.
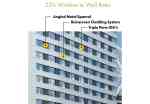
Window Performance
Windows are often one of the largest cost premiums between a Passive House building and a conventional building. Windows are vital for comfort and well-being, but a weak point for thermal conductivity, air tightness, and thermal comfort. In addition, the limited availability of high performing windows, particularly in the US market, has previously limited PH projects to a low overall glazing percentage. Windows at The House were sized to meet building light and air, aesthetic and PH requirements, ultimately leading to 23% glazing area within the façade. The punched windows have thermally broken aluminum window frames by Schuco with a triple glazed IGU with a low-e coating and argon fill. Within the IGU, desiccant-filled warm-edge spacers replace traditional metal spacers. With a whole window u-value of 0.168, The House has some of the highest performing windows available on the market at the time of construction. To avoid excessive solar heat gain on the Southern exposures, the glazing has an SHGC of 0.28.
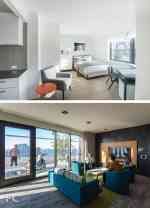
Thermal Comfort Criteria
Extremely high performing windows were also required to meet the PH thermal comfort criteria intended to minimize drafts and temperature stratification formed when conditioned air meets a cold window surface. These high performance windows had the added benefit of eliminating the need to provide heat at the exterior wall offering the design team greater flexibility in laying out the HVAC system, interior wall location and furniture placement. Beyond keeping heat in, the windows, coupled with the airtight insulated façade, also keeps noise out. This is a huge acoustic benefit for The House which stands adjacent to the Queensborough Bridge
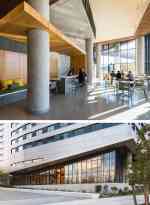
Performance Trade-Offs
It is not always possible or required by the PH standard to have high performing window assemblies in all locations. The ground floor of The House has a large multi-purpose lobby separated from an exterior porch by a storefront assembly that climbs to 23 feet tall. It was prohibitively expensive to meet the same punched window frame u-values and glazing u-values, but this welcoming social space is integral to the campus and urban design concept. The team specified a double-paned thermally broken Oldcastle building envelope system which while higher performing than typical assemblies, required additional perimeter heating to meet PH comfort criteria. The team used hydronic trench heaters in the slab at the storefront base. This lower performing storefront system and energy intensive heating element increased the overall energy demands, but by building up performance buffers within other variables, the team was able to offset the impact and meet the Passive House design criteria.
Thermal Bridge Mitigation
At the detail level, the Passive House energy model considers every thermal bridge in the building. At The House, many common thermal bridges were able to be tightly controlled by the shop fabrication of the panels. For example, to minimize thermal bridging at the window perimeter, aluminum windows were installed so that the integral thermal break is aligned with the continuous insulation plane behind the cladding. A detail like this can be very tricky in the field, but in the shop it was much easier to maintain consistent performance.
One of the largest thermal bridges is inherent to the mega-panel system assembly. The panel joints are a continuous break in the insulation. The design team worked with the fabricator during Design Assist to incorporate new structural high-density plastic thermal breaks at the edges of the panels to interrupt the cold metal cladding from extending to the conditioned interior. Additionally, the panel joint was filled with mineral wool before the sealant was applied to the exterior. Even with these added measures, the resulting R-5 assembly at the panel joint is a significant hit to the cumulative performance of the facade.
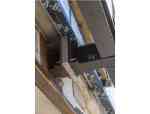
Structural Thermal Breaks
Another repeating thermal bridge occurs at the aforementioned “gills” of the building. Behind these screens are exterior balconies that house the condensers for the low-energy variable refrigerant flow (VRF) mechanical system that heat and cool each floor. At first glance, the concrete floor slab of these balconies appears to simply extend from interior to exterior, creating a major thermal bridge for heat to travel across. Upon a closer look at the detailone can see that this slab is thermally broken by using a structural thermal concrete to concrete isolator by Schock This product is a continuous high-density structural plastic insulation threaded with stainless steel rebar that ties into the structural slab on the warm side of the envelope. Structural thermal isolators from Schock (steel-to-steel) were also employed to mitigate thermal bridging at the ground floor steel-supported canopy above the exterior porch at the ground floor.
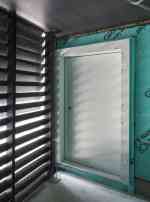
Insulated Doors
These 23 thermally-isolated balconies each required an access door, a major source of heat loss that other variables in the model initially could not offset. At the time thermally broken hollow metal door frames were not readily available, so the team looked to the restaurant industry for a creative solution, installing insulated walk-in refrigerator doors on concrete curbs. This solution was effective thermally and for air-sealing, but it was expensive. It also resulted in lost floor area as each door required a vestibule to combat stack effect, and maintain security. However, these doors allowed the team to save their energy allowance for more visible moments.
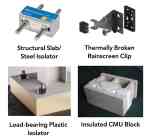
Innovative Detailing
In addition to a highly insulated wall, The House has an R-40 inverted roof membrane (IRMA) roof assembly. High rise roof insulation is frequently interrupted by concrete curbs and steel dunnage supporting heavy mechanical equipment and partitions. The team had to find a structural solution that would minimize heat loss at these penetrations. A high-density load-bearing plastic from General Plastics was employed. These blocks can have compressive strengths that exceed concrete and can be cut to any size and pre-drilled for anchorage. The plastic blocks mitigate these multiple thermal bridges by maintaining continuous insulation, only the steel blocks bridge the insulation plane.
Mechanical Systems
The final set of variables that must be discussed for any Passive House are the mechanical systems. These variables encompass heating/cooling/humidity, as well as building ventilation. The choice of system has direct and indirect impacts on the building façade.
Passive House criteria requires fresh air to be ducted into each bedroom and living room with mechanical exhaust from every kitchen and toilet room. This constant supply of fresh, filtered air provides superior indoor air quality. To minimize energy loss in the ventilation system, exhaust and supply air is required to go through an energy recovery ventilators (ERV), that:
- Extract moisture/humidity and heat out of the outdoor supply air in summer months, and dump it into outgoing exhaust air.
- Transfer moisture/humidity and heat to the outdoor supply air from the conditioned exhaust air in the winter months.
Finding ERV’s large enough and suitable for this project was a challenge. Passive House certified ERVs often meet an efficiency of 80% or greater, but this efficiency could not be achieved at CFM levels required for the building. The team worked with manufacturers to develop a maximally efficient custom solution, with a target efficiency of around 70%. This performance criterium was determined early in the project with PHI and impacted performance targets for several of the previously mentioned façade variables.
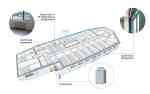
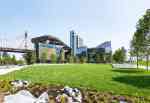
Seeing Results on Roosevelt Island
The House was completed in summer 2017, in time for the first class of students at the new Cornell Tech Campus. The design and construction of the project was a collaborative process with decisions impacted by budgetary restrictions, technological and market limitations, and evolving notions about glazing percentage. Favorable site variables offset limitations in mechanical technologies. Expedited exterior wall construction schedule offset expensive high-performing windows. Innovative products and systems minimized long accepted flaws like thermal bridging and infiltration. Most importantly, the team was able to achieve its design vision without sacrificing occupant comfort all while adhering to some of the most strict whole-building performance criteria in the world to build a building that is projected to save 28.8 million kBtu of electricity per year, the equivalent 882 tons of CO2 or planting 5,300 new trees.
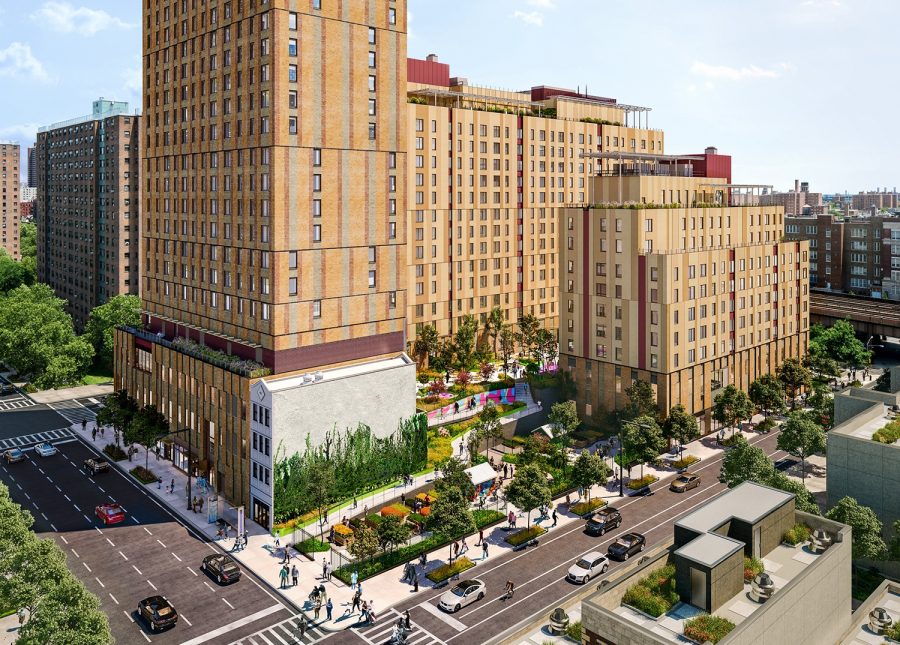
Case Study 2:
Sendero Verde
Sendero Verde is a mixed-use multi-building project awarded through New York City’s SustainNYC competition. Comprising nearly a full city block in East Harlem, the driving concept is to create a "Community of Opportunity" that provides opportunities and support services under one roof, to work to break the cycle of poverty in a community.
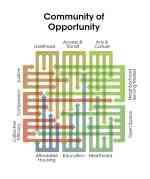
By reducing utility costs and increasing occupant comfort, the Passive House standard is integral to achieving this equitable mission. The 780,000gsf project contains over 700 permanently affordable housing units, outdoor community gardens, retail space, and a robust community facilities program including: a medical office, school, and a senior and student support center. All programs are linked by a connection to a privately-owned public green space that includes a central meandering landscaped path. The massing is broken into three volumes which frame this path, creating a central courtyard. Construction began in July 2019 and when it is completed Sendero Verde will be the largest fully affordable Passive House building in the world.
Site and Program
Sendero Verde (SV) is comprised of three buildings with multiple programs:
SVA:
383 residential units in 37-stories at the corner of Madison Avenue and East 112th Street. Community facilities include: medical office, art gallery, and ground floor retail. The structure is cast-in-place concrete.
SVBn:
276 residential units in 15-stories along E 112th street from SVA to Park Ave. Community facilities include: the privately owned public green space at the center of the development, social services offices, and a charter school. The structure is cast-in-place concrete.
SVBs:
85 residential units in 10-stories building mid-block on E 111th street. Community facilities include: non-profit senior and student services. The structure is load-bearing concrete block and precast plank.
The buildings will be built in two phases with SVBn and SVBs under construction now, and SVA following in 2020.
The project’s development team includes Jonathan Rose Companies, L+M Development, and the Acacia Network. As the three buildings are separated and do not share systems, PHI requires each building to be modeled independently.
Since the compactness of each building varies, it was clear from the start that variable inputs would be very different for each building. SVA and SVBn which are much larger and more compact with conditioned volumes of 2.6m ft3 and 1.9m ft3, respectively, began PH modeling in a more advantageous spot than the less compact SVBs with a conditioned volume of only 590k ft3.
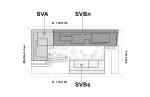
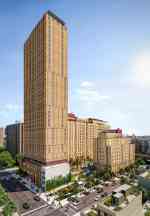
Urban Context
Sendero Verde’s urban context means that unlike at Cornell Tech’s The House, the design team was not able to optimize site variables like orientation and massing. To maximize sunlight in the landscaped areas, larger building massings were pushed to the Northern edge of the site. The result is significant Northern and Southern exposures, set slightly off axis by the Manhattan grid. SVA is the tallest building within a multi-block radius and has an L-shaped massing to maximize the efficiency of the interior layout. The result is large Eastern and Western exposures with direct sunlight in mornings and evenings. The variation of solar heat gain across the site meant that using typical glazing and exterior wall assemblies site-wide would require several carefully calculated zones for the mechanical systems.
Sendero Verde has an ambitious program in an urban context that could further challenge the project’s sustainability goals. As a “community of opportunity” the project must house multiple different tenants. The various unknowns surrounding each commercial and nonprofit tenant’s fit out, lead the design team to opt to seek PH certification for only the residential program of each building.
Surrounding the block, the urban and historic context also put pressure on the design team. East Harlem is a neighborhood filled with vibrant murals and outdoor markets. It is also home to several mid-century New York City Housing Authority (NYCHA) residential developments, compact towers with uniform brown brick facades sitting amidst unprogrammed green lawns. The challenge was to create a dynamic façade and building massing to disassociate Sendero Verde from past attempts at affordable housing, without creating conditions that would harm the project’s performance and budget like excess corners, cantilevers, and large glazed areas. The design team employed proportional systems, color, material textures, varying brick cavity depths, and greenery to create a project that the community would be excited to move around and through.
Exterior Wall
The affordable housing project’s limited budget called for conventional building materials and construction techniques. The quality control and efficiency of the shop-fabricated panel system used at The House was out of the question. To provide a cohesive pedestrian experience, the lower floors of each building are clad in a two-color hand-laid brick veneer, with generous storefront openings marking each residential and community partner entrance. Except for residential lobbies, this podium is outside the thermal requirements of the Passive House envelope. To facilitate construction and energy efficiency even at non-PH areas, the entire façade is designed to meet air tightness criteria.
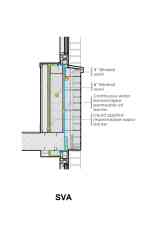
SVA Wall Assembly
As the tallest building, SVA has the greatest compactness ratio but is subject to the worst wind loads. While the site variables afford the design team more tolerance in the PH energy model, the exterior cladding was subject to the largest structural stresses. For these reasons a brick veneer cladding was selected. Creating an airtight envelope and minimizing thermal bridges with hand-laid brick veneer brought significant challenges. The backup wall was designed with heavy gauge 6-inch steel studs. Stud cavities were filled with 6” of mineral wool insulation and another 3” was laid continuously in the brick cavity. The result was an R-24 wall assembly after de-rating the insulation’s thermal performance to account for thermal bridging at brick ties and steel studs.
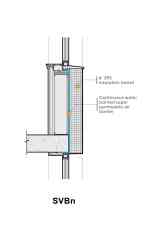
SVBn Wall Assembly
SVBn & SVBs are shorter buildings, subject to lower wind loads and set back from Madison and Park Avenue. The team chose a more cost-effective EIFS (exterior insulated finish system) assembly with 6” of continuous EPS insulation in front of a continuous air barrier and drainage plane. In addition to reducing cost, EIFS provides continuous insulation with no mechanical fasteners or supports, and the only interruption occurs at movement joints. SVBn has a steel stud backup wall identical to SVA, but due to low S/V ratio and the limited thermal bridging inherent in the EIFS assembly, it meets the performance goals without insulation in the stud cavities. The result is an R-22 exterior wall. Architecturally, the EIFS façade is designed with an active pattern and colors to engage the residents and provide visual interest.
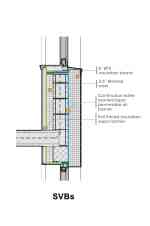
SVBs Wall Assembly
With higher S/V ratio starting SVBs off at a big disadvantage, the EIFS cladding alone did not provide adequate thermal performance. To further complicate matters, SVBs is a block and plank structure with CMU walls and no stud cavities to fill with insulation, so insulation was added to the interior side of the wall, thus decreasing leasable floor area. The team studied manipulating other variables like using higher performing windows, but it was more cost-effective to add insulation and sacrifice floor area. 3 ½” of continuous mineral wool insulation is pinned behind a furring wall service cavity at the exterior perimeter resulting in an R-40 exterior wall.
Due to the limited roof surface area on SVA, it was determined there was little benefit exceeding the NYCECC code minimum R-30 roof. SVBn also has an R-30 roof as the high performing windows and wall left a buffer in the energy budget. However, the less compact SVBs, again with its higher S/V ratio required an R-40 roof assembly.
Air Sealing
While the non-residential program was removed from the PH certified area, it was determined early in schematic design that it would be difficult to expect to maintain and verify effective air seals at the program transitions and thus, the entire façade is designed to meet the Passive House air tightness criteria, and only the certified spaces were required to meet the thermal requirements. This required continuous air sealing details to be developed for all façade conditions, not just those in certified areas.
The Sendero Verde air barrier will be field-applied and all penetrations will need to be controlled and sealed in the field. To ensure the results required by PH the design team took the following measures:
- Developed taping and sealant details for door and window openings.
- Pipe and conduit penetrations are sealed with vapor permeable gaskets.
- All inactive louvers have insulated blank off panels with continuous tape at the perimeter.
Unlike The House, the primary air seal on each SV building is a vapor-permeable air barrier and waterproofing membrane applied directly to the exterior side of the backup wall. This allows redundancy between the air barrier and exterior wall waterproofing which would already be installed and sealed by the cladding contractors. For SVBn, this one AVB is all that is required. However, because SVA and SVBs have insulation on the interior side of the primary AVB they both require a second vapor barrier, for similar vapor control reasons to The House. SVA, uses a roll-on vapor barrier on the interior face of the steel stud backup wall, while on SVBs the interior mineral wool insulation is foil-faced with continuous taping at joints and slabs.
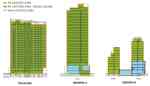
Window Performance
To keep cost and performance requirements in check, and guided by code requirements for light and air, window area is an average of 21% across the three buildings. Due to the height and wind loads for SVA, thermally broken aluminum windows have been specified. SVBn and SVBs have less stringent wind load requirements and are closer to the Metro North commuter train overpass along Park Avenue, so uPVC frames were selected to provide higher thermal and acoustic performance at a lower cost. All glazing is triple pane with low-e coating, argon fill and warm edge spacers.
At The House, the design team engaged in Design Assist with the panel fabricators allowing near total control over the actual installation details of the windows and a clear understanding of the exact performance requirements required for window components (frame, glazing, and spacer). SV is following the design, bid path. To maintain competitive pricing, the design team developed specific installation details for the head, jamb, and sill, and prepared a detailed performance specification with requirements for the other components based on the performance of the installation details included in the bid drawings. The result is a small-scale performance-based standard. A window manufacturer bidding the job can meet every requirement as written or offset worse performance in one component by higher performance in another. They can even propose lower performing components overall offset by revised install details with better thermal performance than those included in the design documents. This method allows the market to assist the design team in finding the most economical solution to meet their performance requirements.
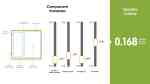
Window Install Details
Each SV building’s install details are unique due to several variables, from massing to building structure and cladding system.
The install details for SVA result in an uninstalled window u-value requirement of 0.149. To minimize thermal bridging the thermal breaks in the aluminum frames had to be aligned to the insulation plane which meant the windows are not sitting on the backup wall below but hanging out in the brick cavity. To support the window’s dead load, blocking wrapped in the air barrier projects from the window sill. Construction sequencing and air sealing were the primary complications at the window jambs. To avoid a thermal bridge the brick veneer had to overlap the window frames allowing the cavity insulation to nestle directly up against the window assembly. However, the pre-construction team made it clear the brick veneer had to be built before the windows were installed. This meant the installers would be unable to seal the window jamb from the exterior since it would be behind the brick veneer. The final detail incorporates a silicone closure piece sealed into the window opening that remains exposed once the brick veneer was installed but is covered by the window. SVA’s window head detail is discussed further in the “thermal bridging” section
SVBn and SVBs have much simpler installation details. The low conductivity of the uPVC frame allows it to be installed with the face of frame aligned to the insulation plane allowing the window to sit entirely on the backup wall. Likewise, since the windows can be installed first, the window frame can be fully sealed and then overlapped by the EIFS cladding, further mitigating heat loss through the frame. The major window-related difference between two buildings is at the head detail. Due to differences in the structural system, SVBn’s window head extends to the underside of the floor slab resulting in decreased thermal performance. The install details for SVBn and SVBs result in an uninstalled window u-value requirement of 0.143 and 0.138, respectively. Lower values that are more easily achieved with uPVC frames.
To maintain consistent aesthetics, the design team specified the same glazing across all buildings. The low-e coating was selected to take advantage of the solar exposure, with a relatively high SHGC of 0.38. This detail contradicts the logic of many prescriptive codes. For example, NYCECC currently limits SHGC to 0.4 and is expected to further lower that number in the next version. The logic here is that limiting heat gain limits cooling load, but in this case the PH model determined there was a net energy benefit to gaining more heat in the winter to offset heating demand.
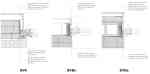
Thermal Bridge Mitigation
On SVA, the most complicated thermal bridge occurs at the brick shelf angles. By locating the shelf angles at the face of each floor slab, the team saved on structural costs, but caused a major thermal bridge. The angles penetrate the cavity insulation and make direct contact with the edge of slab. Complicating the detail further, this is also the location of the aluminum window heads. This detail jeopardized the thermal performance of the wall and compromised the thermal comfort criteria by making the interior surface of the window frame cold enough to pose a condensation risk. To mitigate this bridge, the team initially looked at offset shelf angle systems from Fero and Halfen. However, a more cost-effective solution that achieved thermal performance is setting the angles a min. of ¾” from the face of slab and providing a structural thermal shim with an R-value of 0.9/in at each attachment point. Then the intermittent spaces between shims are filled with spray foam insulation. On a small project this detail could be unique and expensive, but the economy of scale afforded by larger projects made this detail feasible.
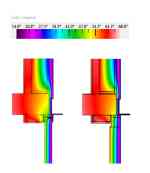
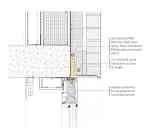
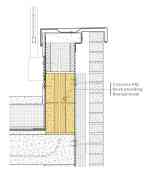
Cutting Cost with Thermal Breaks
Another innovative approach to thermal bridge mitigation can be seen at the rooftop parapets on all buildings. To meet the prescriptive code minimums for roof assemblies, parapets are often wrapped in insulation. This is costly and difficult to construct. Using THERM modeling the design team determined that the same thermal performance could be achieved with an uninsulated parapet that was supported on Autoclaved Aerated Concrete block (AAC) block curbs in lieu of cast-in-place concrete or typical CMU. AAC is made with finer aggregates, cement, and an expansion agent that results in a block that is 80% air, thus making it an excellent insulator that is also strong and fire resistant. After developing the typical parapet detail, AAC block is employed in several details in lieu of structural curbs for roof equipment and roofing terminations, much the way the General Plastics product was used at the House.
With thermal bridge mitigation, as with other aspects of PH design, the SV team benefitted greatly from the firm’s experience at The House.
The team used several similar details to minimize thermal bridging including:
- Rooftop dunnage and continuous equipment curbs were built on structural plastic thermal isolators.
- Canopy support steel was thermally broken with structural steel-to-steel isolators at PH envelope locations
- Concrete floor slabs at the SVA exterior condenser balconies were supported on continuous concrete-to-concrete thermal isolators.
As more PH projects come online, manufacturers are bringing new materials to market. For example, thermally broken door frames are now readily available which made the extremely expensive refrigerator doors used on The House unnecessary at the SVA condenser balconies.
Mechanical Systems
When compared to The House, one of the most impactful variables is the efficiency of the ERVs.
The design team pushed ERV manufacturers to develop a custom unit with an efficiency of 80%, and by improving the ERV efficiency, the design team was able to take some pressure off other variables. For example, we have more allowance for thermal bridging conditions at shelf angles and de-rated insulation in stud cavities. This exemplifies the benefits of performance-based standards. As technologies improve in one area the benefits can be shared across multiple variables.
Efficient VRF mechanical systems in concert with a heavily-insulated, air tight exterior wall significantly reduce energy consumption which will convert to lower utility bills for residents of Sendero Verde. This plays an integral role in meeting this community of opportunity’s goal to promote equity in the reduction of carbon emissions by bringing the benefits of energy efficient and comfortable buildings to low-income residents in an underserved neighborhood.
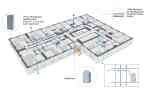
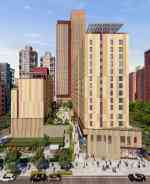
A Community of Opportunity
Building on the firm’s experience at The House and advancements in building systems the team developed new approaches to building practices to create a cohesive Passive House project.
Site conditions vary by building, as do the impact of decisions on exterior cladding and window systems. While cost is a major driver in all decisions, the performance-based criteria and data driven approach of PH ensured building performance was never value engineered.
Once completed Sendero Verde will be one of the largest PH certified residential buildings in the world, but it will also be a new community of opportunity providing neighborhood services and affordable housing to thousands of New Yorkers.
Next Steps at Handel Architects and Beyond
The House at Cornell Tech and Sendero Verde are designed to meet the exact same performance criteria, but you would never know by looking at them.
Using the Passive House standard, Handel Architects and their partners designed two projects that successfully met the programmatic, aesthetic, budgetary, and contextual demands of their clients while using less energy per square foot than almost any other building in the country. The House paved the way for numerous high-rise Passive House developments popping up across New York City. Sendero Verde looks to build on that success with a community-based approach that addresses equity in the reduction of carbon emissions.
Multi-family high-rise developments like The House and Sendero Verde are just one of the recent successes of the Passive House standard. At a time when governments and private clients around the world are seeking to decrease the carbon footprint of their building stock, the adaptability of this performance-based system makes PH an ideal standard for future energy efficient buildings. PHI is continuously working to implement the PH standard in new climates and typologies. In 2018, Star Garment Innovation Center, designed by Vinod Jayasinghe Associates became the first PHI certified manufacturing facility in Sri Lanka. On the other side of the world in downtown Boston Handel Architects is designing its first Passive House office building. The Winthrop Square tower features 4 stories of public non-PH program area with a 21-story, 735,000gsf office program that will seek PHI certification beneath 30-stories of non-Passive House luxury residential condominiums. This project will feature a highly insulated, air-tight, unitized curtain wall with 45% glazing, compared with the 23% at The House and 21% at Sendero Verde. Even further North, Handel Architects is in early design stages for their fourth project to seek PH certification, a new dormitory and student center for a prestigious Canadian university. Due to the colder climate zone, the performance criteria is markedly different from The House, a similar program. Due to the high density and extreme climate zone, the max EUI is 70.5 kBtu/sf/yr.
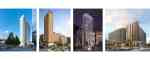
In addition to advancing the Passive House mission, these projects are impacting the larger building industry by pushing manufacturers to rethink the market for highly efficient and sustainable products.
Thoughtful examination of different variables has led Passive House design teams to push manufacturers for products that simply don’t exist at scale in the US market like mineral wool based EIFS assemblies, large-capacity high-efficiency Energy Recovery Ventilators (ERV), extremely low-capacity VRF evaporators, and triple-pane thermally broken unitized curtain wall. Meanwhile at the detail scale, these projects implement new technologies for eliminating thermal bridges and improving air tightness including: load-bearing plastic thermal breaks, structural thermal isolators, aerated autoclaved concrete masonry units, variable-perm air and vapor barriers, vapor permeable gaskets, air barrier tapes, warm-edge IGU spacers and more. Embodying the notion that “a rising tide lifts all boats”: these technologies have now seen wider use on other projects within Handel Architects, even those not seeking PH certification.
The success of projects around the world using performance-based standards like Passive House are pushing energy codes and legislative mandates to incorporate more performance-based requirements and focus in greater detail on those areas that have the greatest impact on overall energy performance like thermal bridging and air tightness. This is building the bridge to the net-energy-neutral, and even net-energy-positive buildings of the future. As building codes continue to evolve, Passive House level performance will rapidly move from a sustainable market niche to a building code minimum (Mann, 2019).
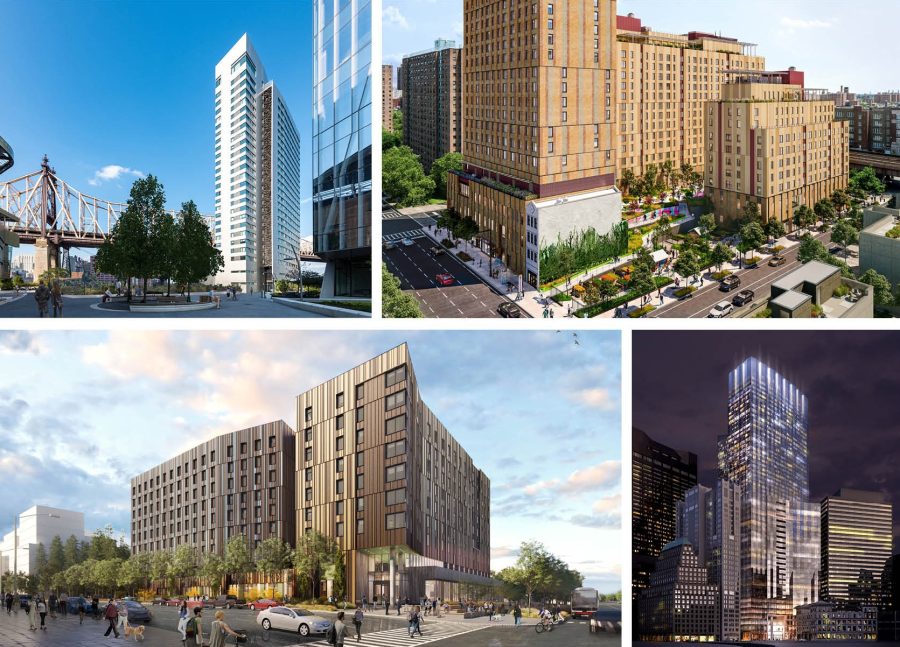
Learn more
View the next report in our series: Sustainability Report Issue #2: Why Passive House Dormitories Are Healthier and More Energy Efficient