Using Computational Tools to Create the Ceiling at Winthrop Center's Connector Space
In order to create the complex folded ceiling at Winthrop Center, the Design Technology team at Handel Architects used a variety of computational design and parametric design tools.
Located in Boston's Financial District, Winthrop Center is a 1.8M sq. ft. mixed-use project including residential, office, and retail. A grand new public space called The Connector anchors the building and traverses the site between Federal and Devonshire streets, offering the public a grand, multilevel "urban room."
A dramatic folding ceiling extends through the space and visually connects the building entrances. Its design evokes the neighborhood's surrounding Art Deco architecture with an angular repeating form, reinforcing The Connector as an addition to the streetscape. Elemental materials of stone, metal, terrazzo further lend the space a sense of robust permanence.
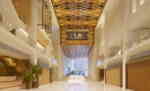
Winthrop's signature ceiling was designed using Rhinoceros3D and Grasshopper.
Grasshopper's parametric capabilities gave the designers greater control over the aesthetics, allowing for fine-tuning of the form while maintaining both visual harmony and functional efficiency.
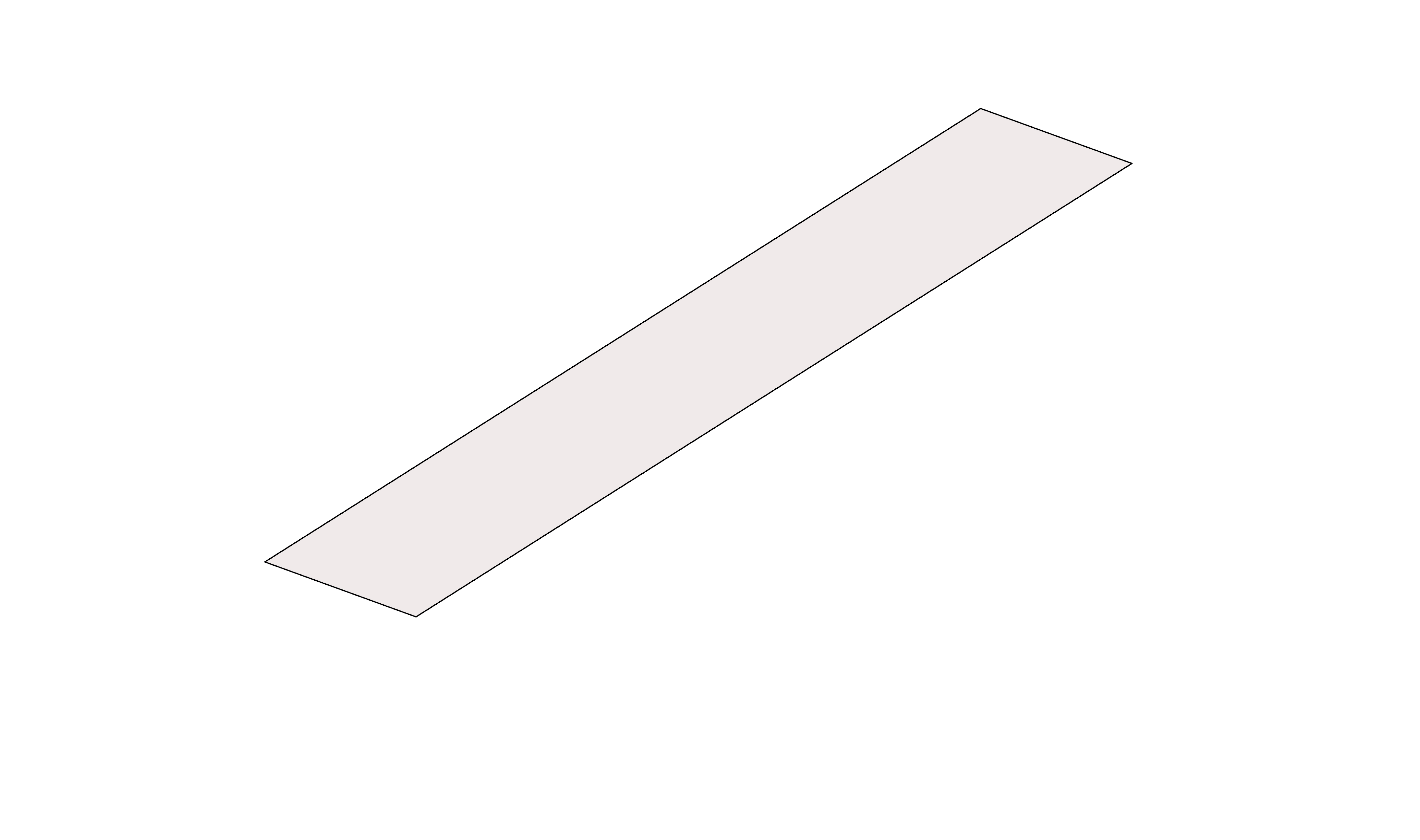
A diagonal grid was applied to the ceiling surface geometry, with iterations of varying spacing increments being parametrically generated and evaluated.
This approach allowed for a rapid and efficient exploration of design possibilities, optimizing both the visual and structural aspects of the ceiling.
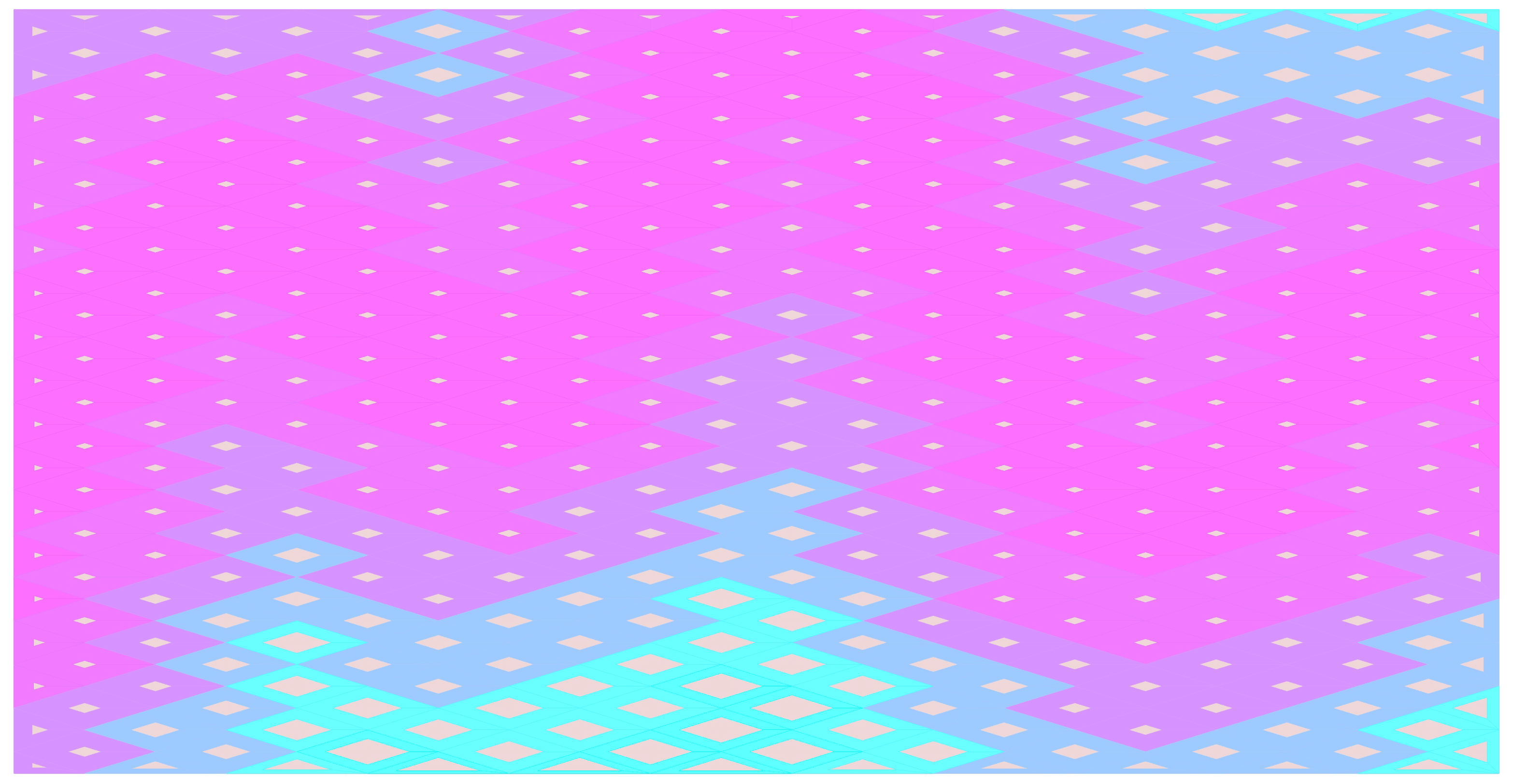
During the formation of the diagrid, various patterns were overlaid onto the ceiling structure.
These patterns introduced a sense of rhythm and flow to the ceiling's design, while also strategically providing openings to accommodate various building services such as lighting, ventilation, and sprinklers. This approach balanced both aesthetics and functionality, ensuring the ceiling was visually dynamic while supporting essential infrastructure.
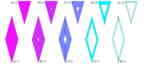
Each color in the design explorations represents a different panel type, with varying opening widths.
These color-coded panels allowed the design team to quickly visualize and differentiate between the options, facilitating a more efficient comparison of the structural and aesthetic impact of each variation.
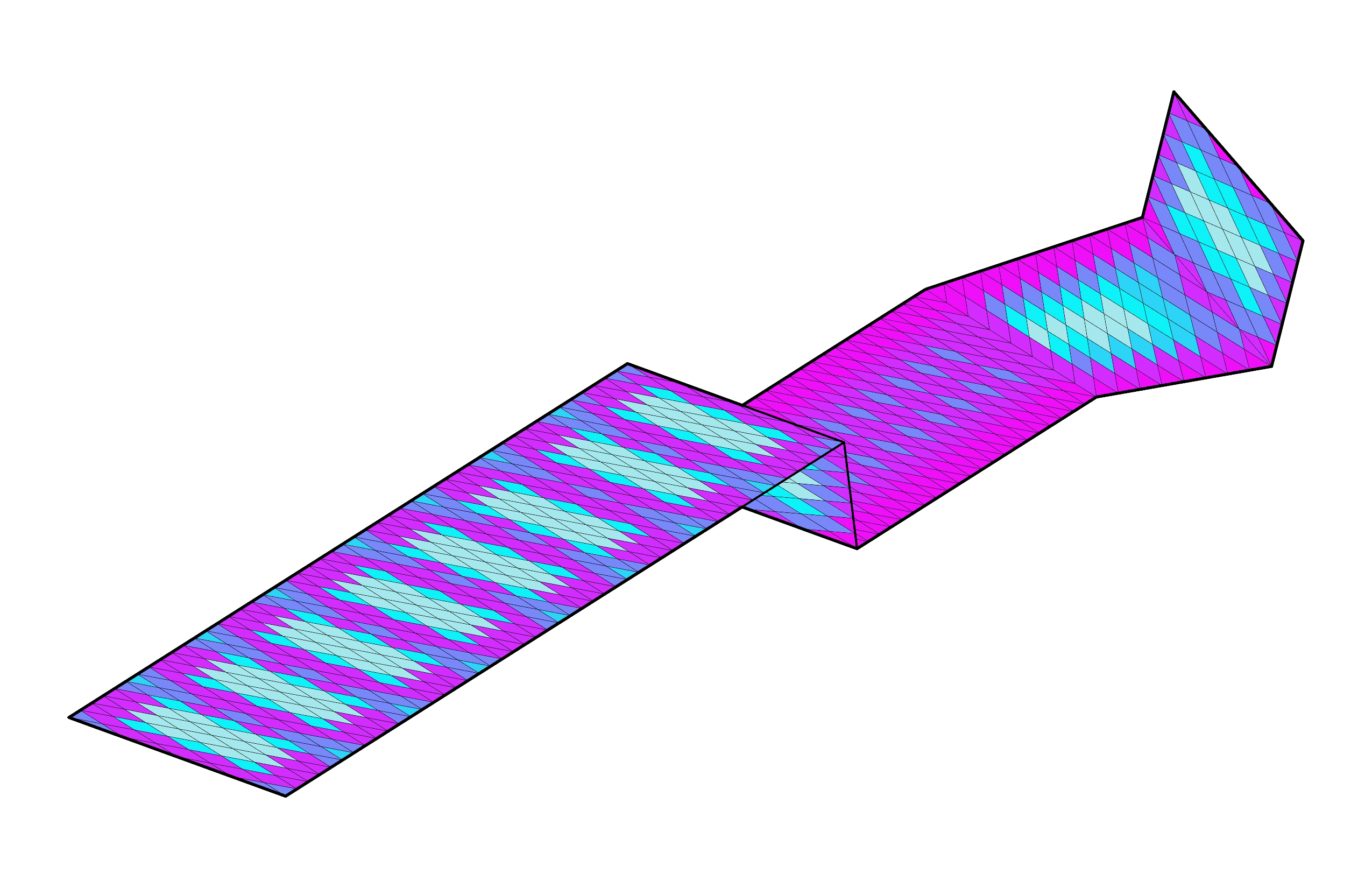
After the design was evaluated, a detailed 3D model was created to further refine and visualize the final structure.
This model allowed the design team to analyze how the various patterns and panel types interact in a real-world context, ensuring that the final product would meet both aesthetic and functional goals. The use of 3D modeling also helped identify any potential issues with the integration of building services and structural elements.
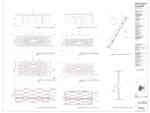
Shop drawings were created in house, ensuring faithful reproduction of design intent.
Following the creation of the 3D model, it served as the foundation for the project's documentation. The model was used to generate detailed drawings, specifications, and construction documents, ensuring that the design intent was clearly communicated to the construction team. This process streamlined the transition from digital design to physical realization, allowing for accurate fabrication and installation of the ceiling structure while minimizing errors and discrepancies during construction.
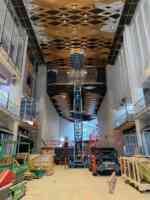
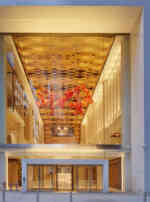